From Short Runs to Lights-Out Manufacturing
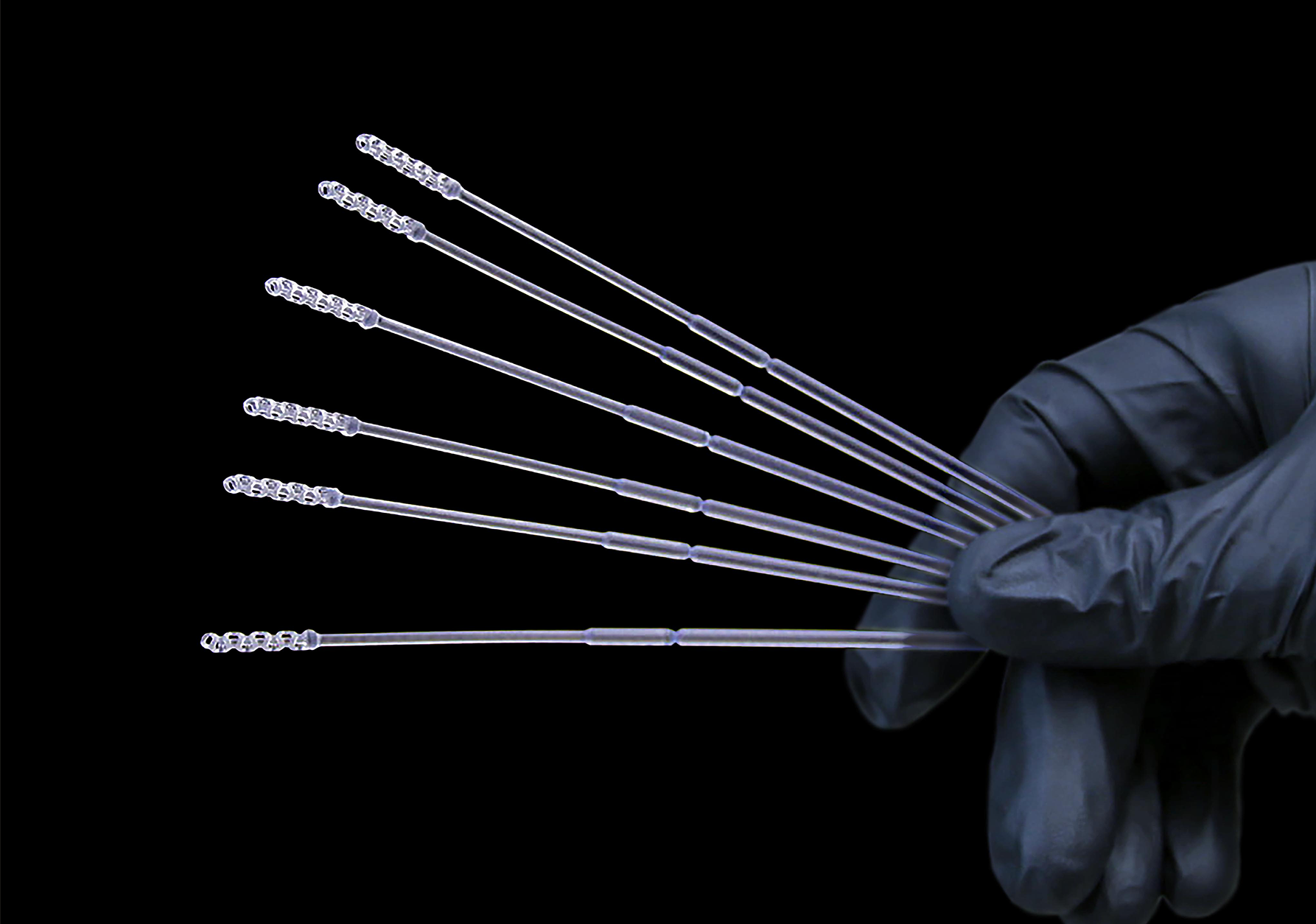
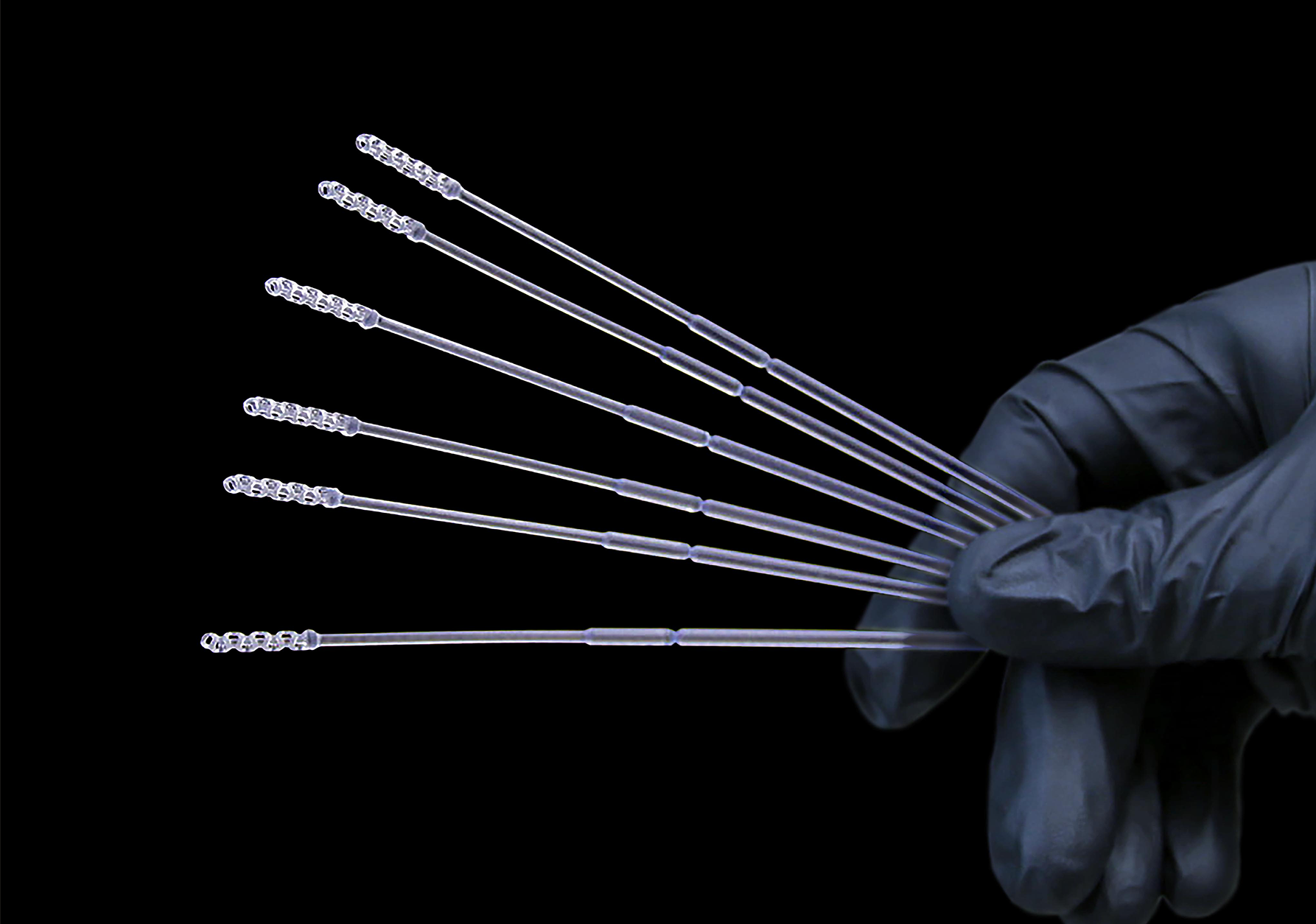
Today’s life sciences sector is characterized by feature-rich designs, shorter product life cycles, and increasingly challenging functional requirements. With part costs, build speeds, accuracy, surface finish and material properties rivaling injection molding, ETEC is disrupting traditional manufacturing of medical products. For the life sciences sector, additive manufacturing is a game changer – delivering unprecedented design creativity and business transformation through tooling-free manufacturing and a dramatically streamlined supply chain.
Whether you’re looking to produce thousands of medical instrument panels, hundreds of thousands of hearing aids or millions of nasopharyngeal swabs, ETEC’s printing systems and materials enable additive manufacturing of the broadest range of parts featuring ultra-fine features, incredibly crisp details, and best-in-class performance.
For more information on ordering nasopharyngeal swabs, contact [email protected]
Industry-leading Materials
Through in-house developed proprietary materials and strategic partnerships with leading materials suppliers, ETEC’s library of 190+ materials covers the industry’s broadest application space, including biocompatible materials; silicones and rigid materials with cytotoxicity, irritation and sensitization data; and optically transparent materials.
Superior Part Economics
With best-in-class build volumes and throughput, ETEC printers produce superior parts faster, and at a lower cost, than conventional manufacturing methods.
Streamlined Supply Chains
With ETEC, you can match production rates to demand, minimize shipping and warehousing costs, and eliminate tariffs.
Trusted by the industry
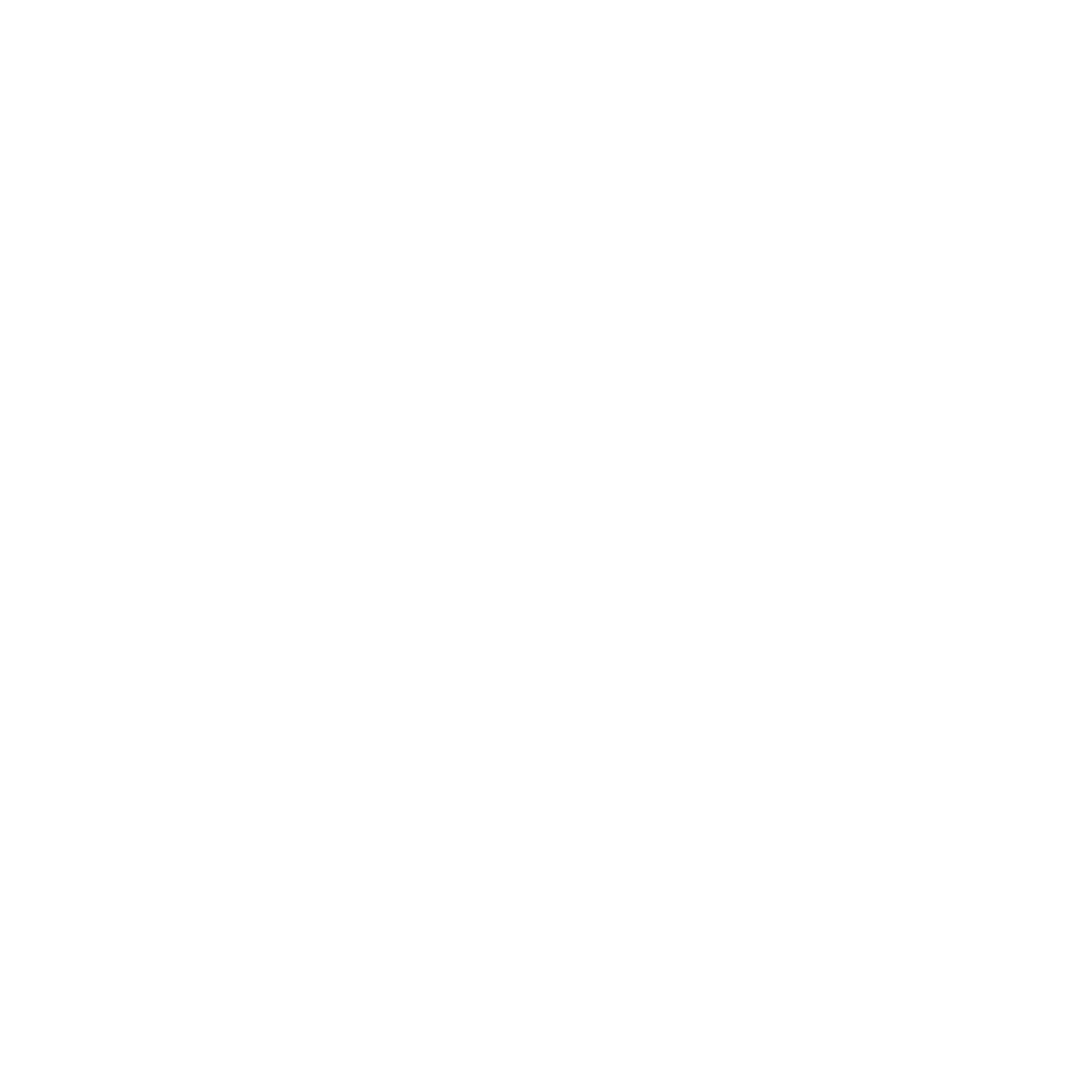
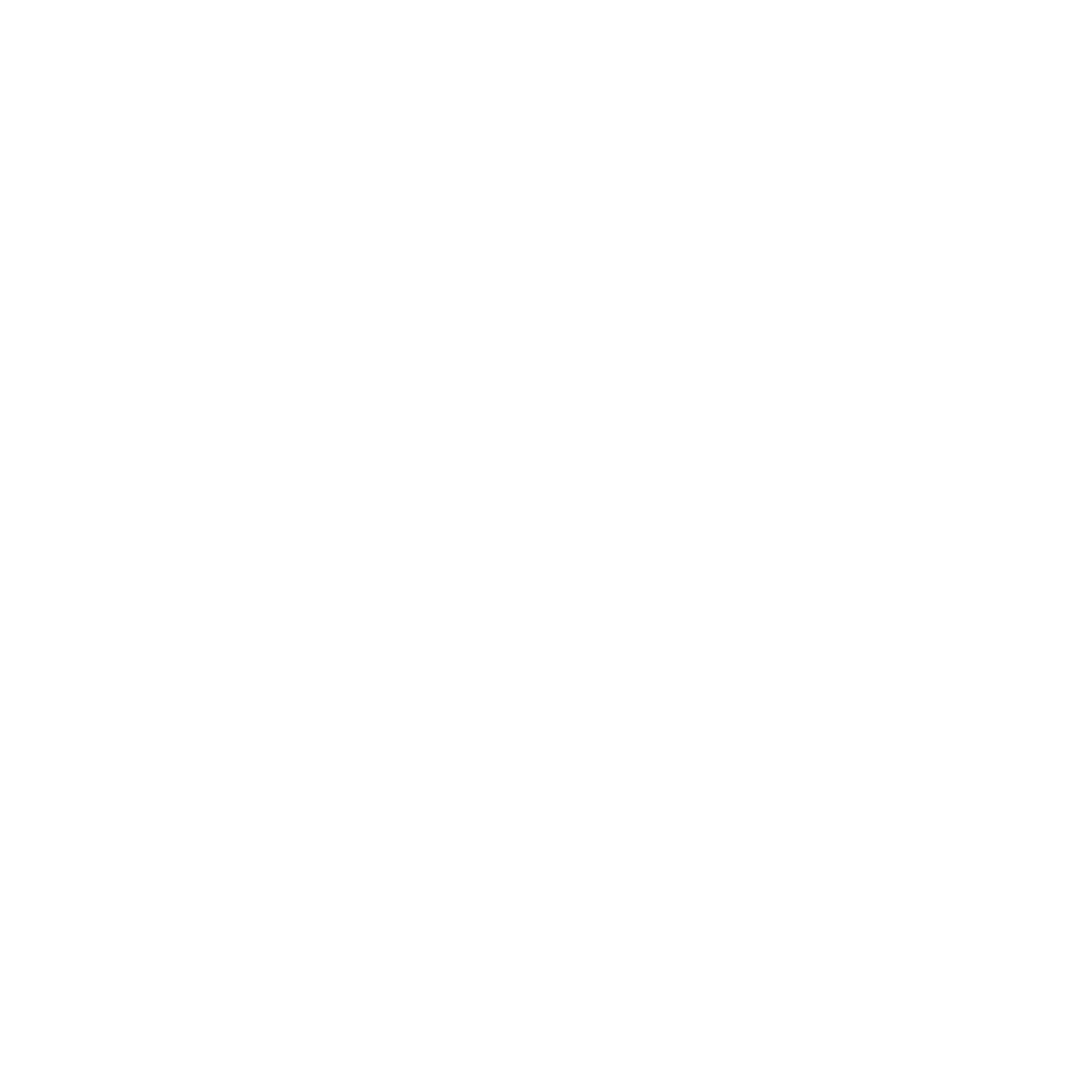
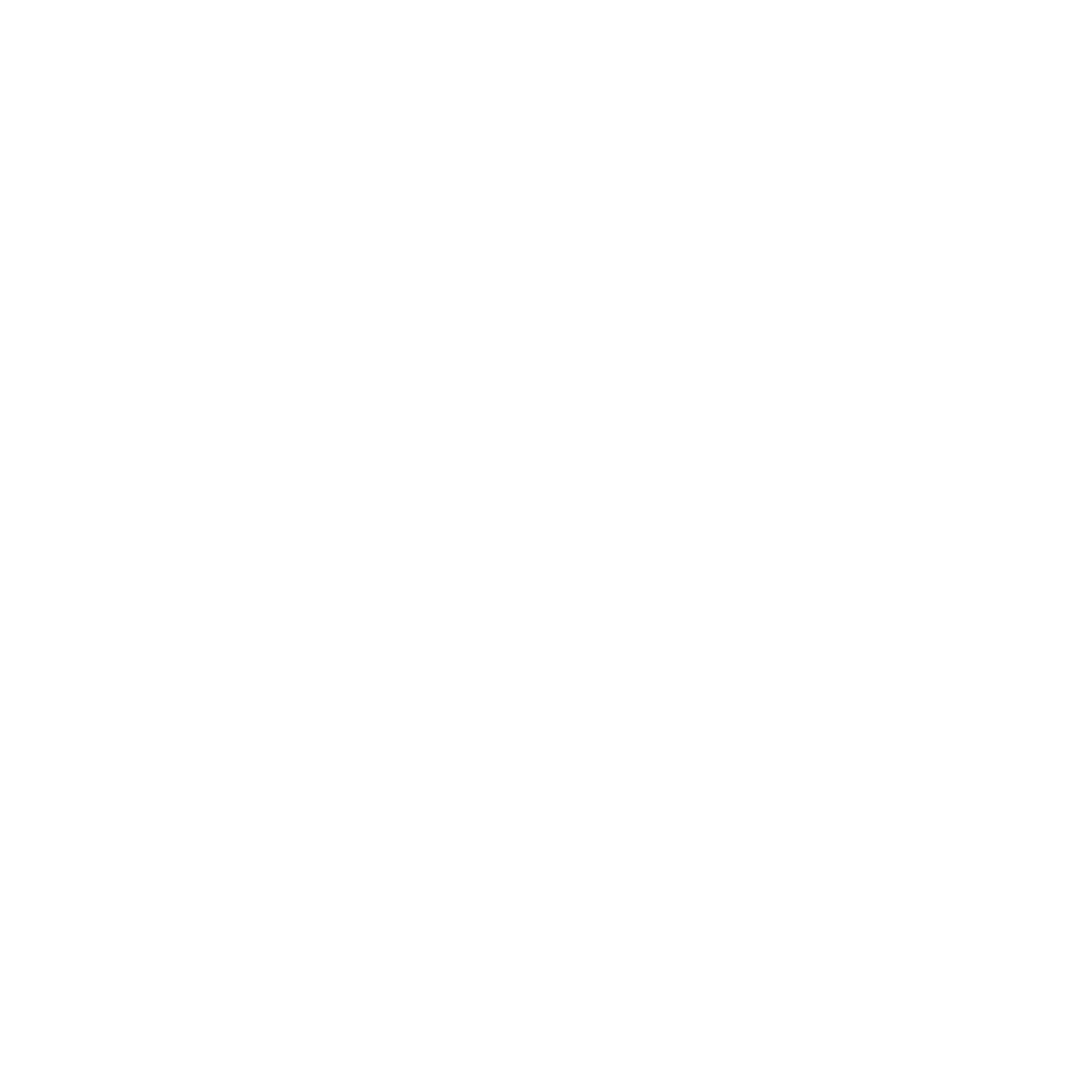
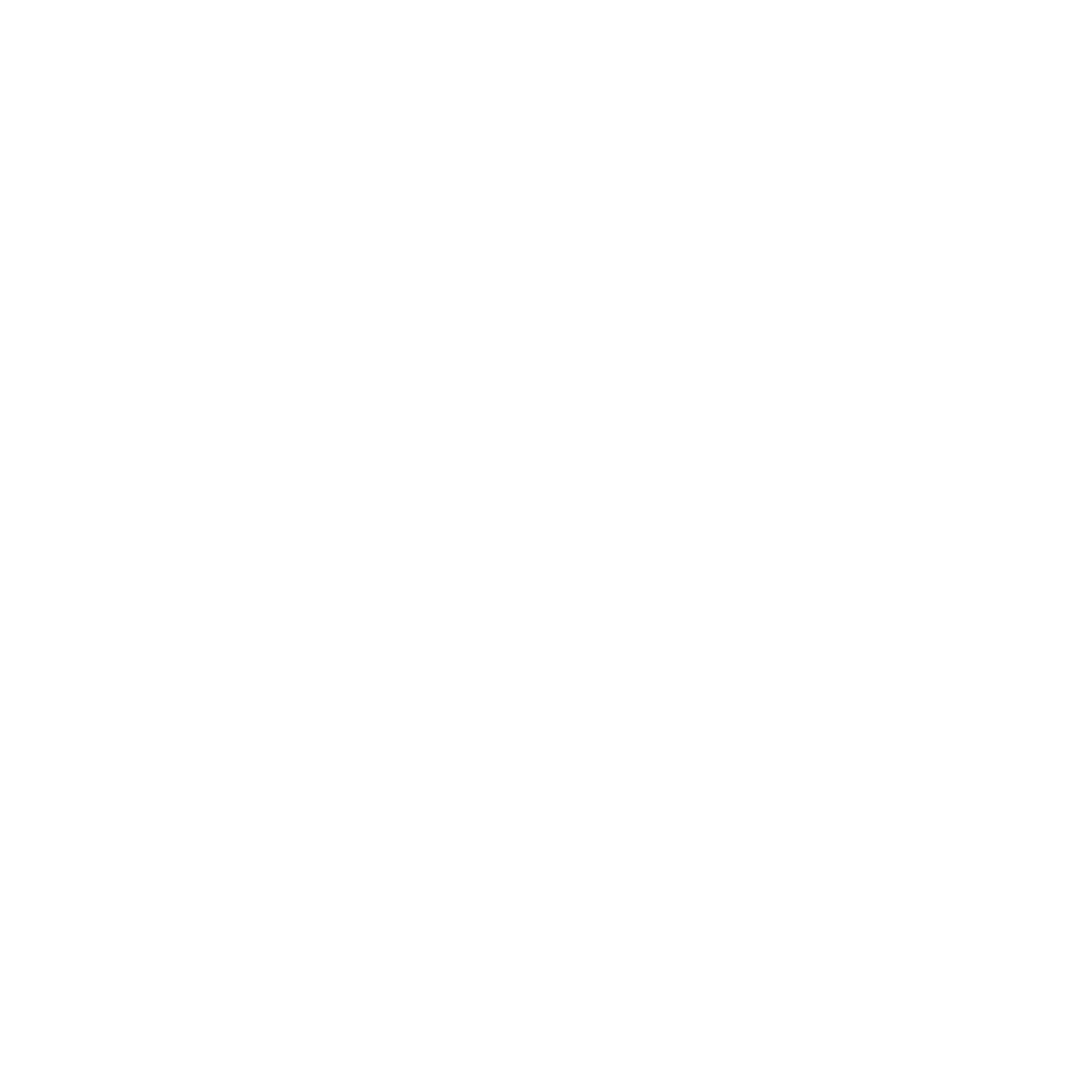
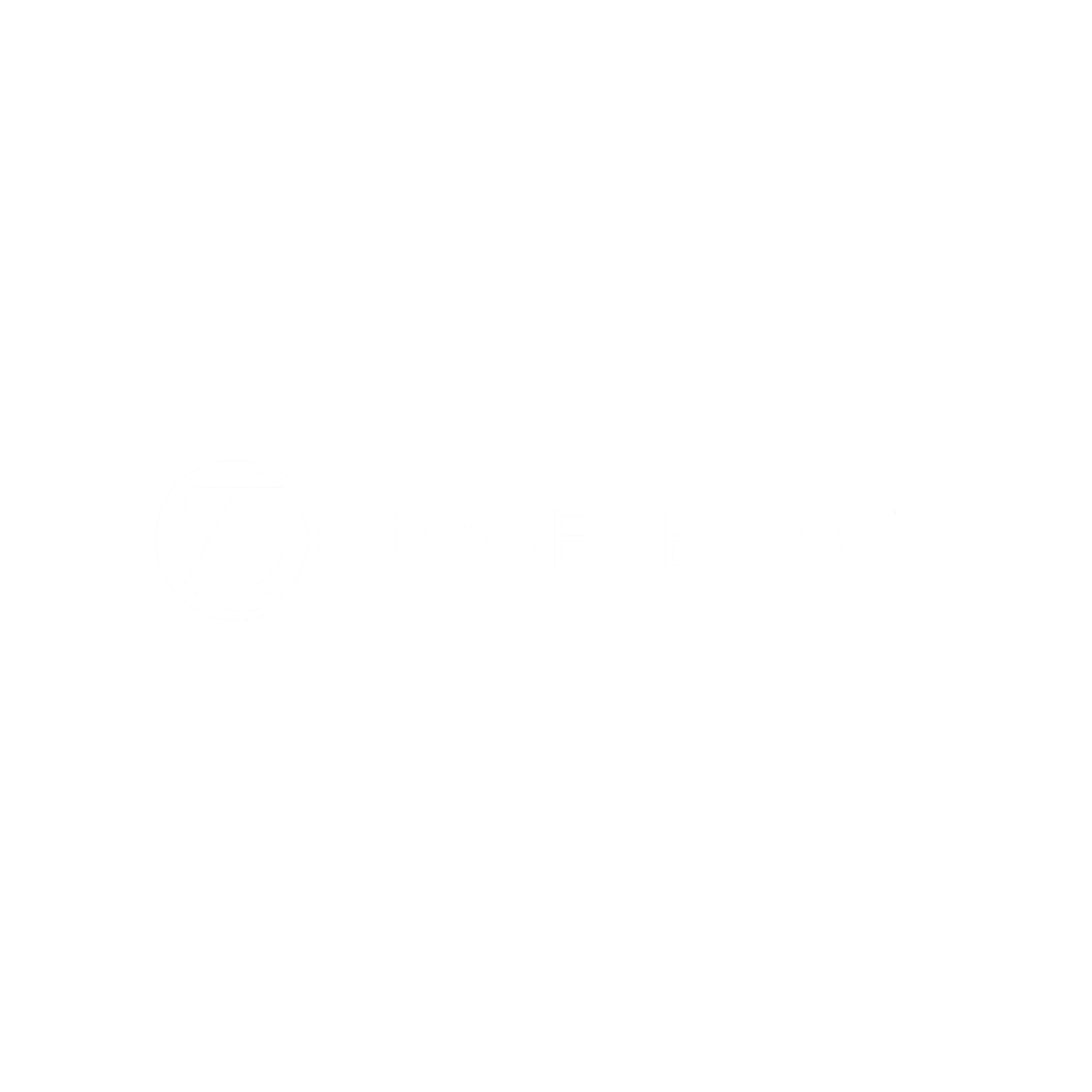
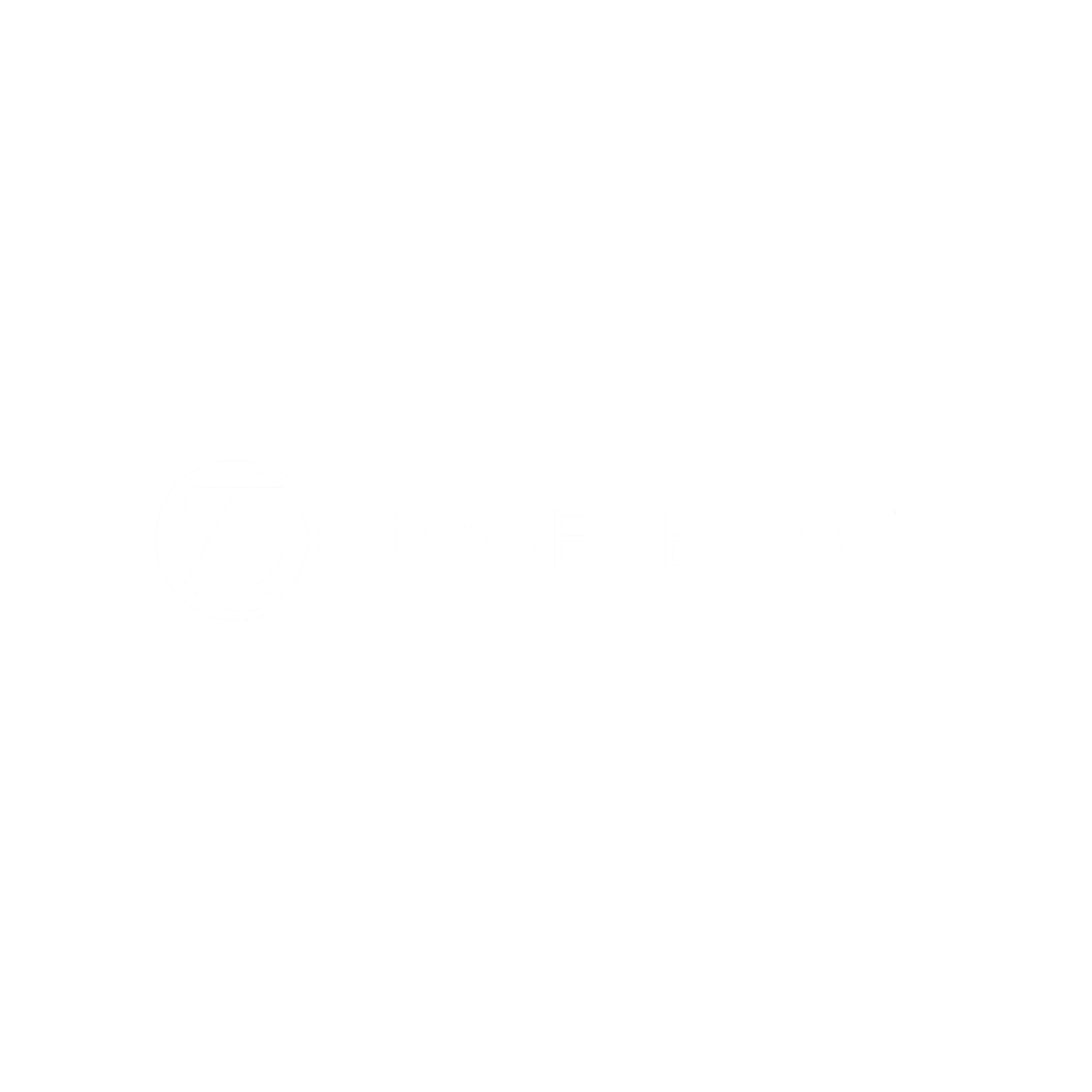
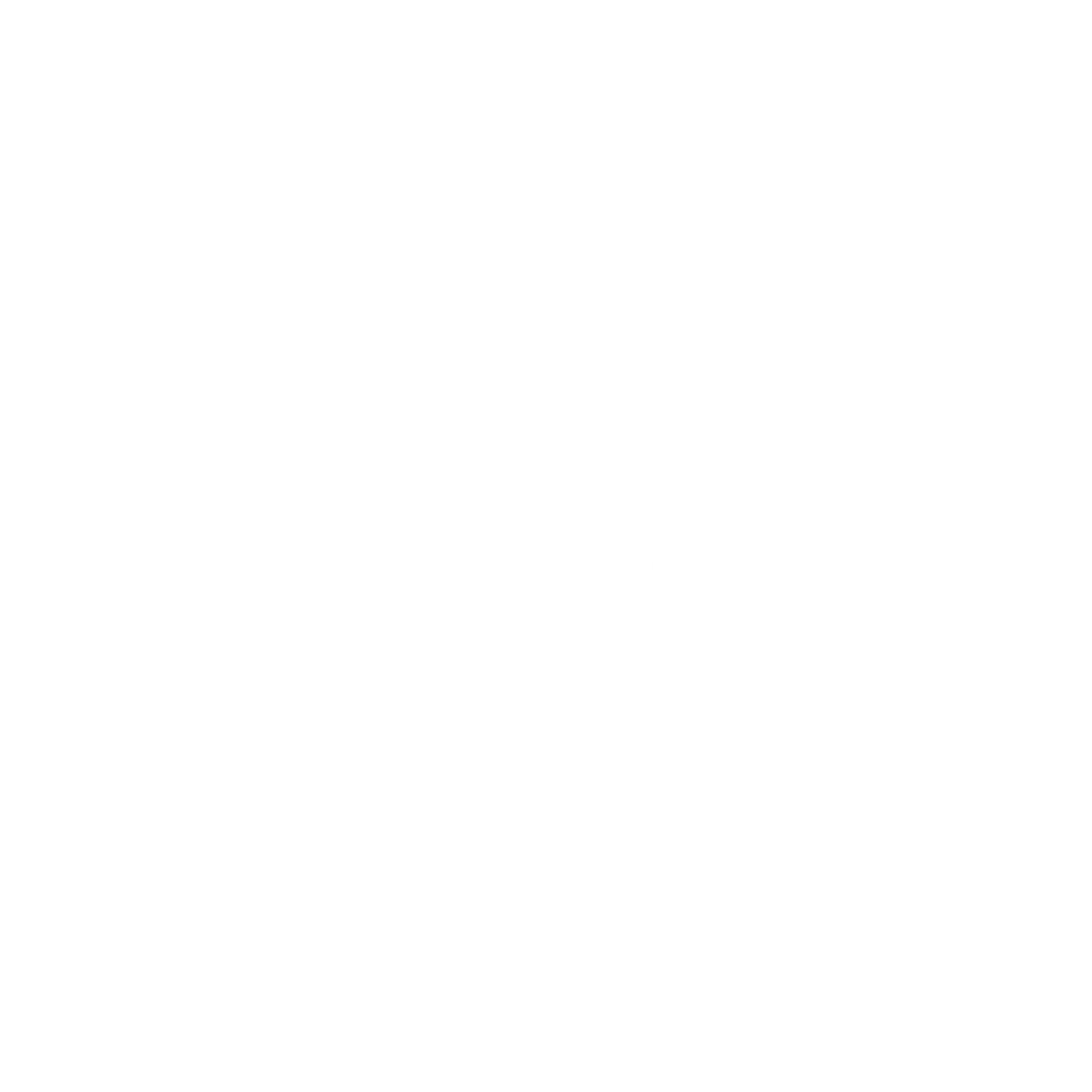
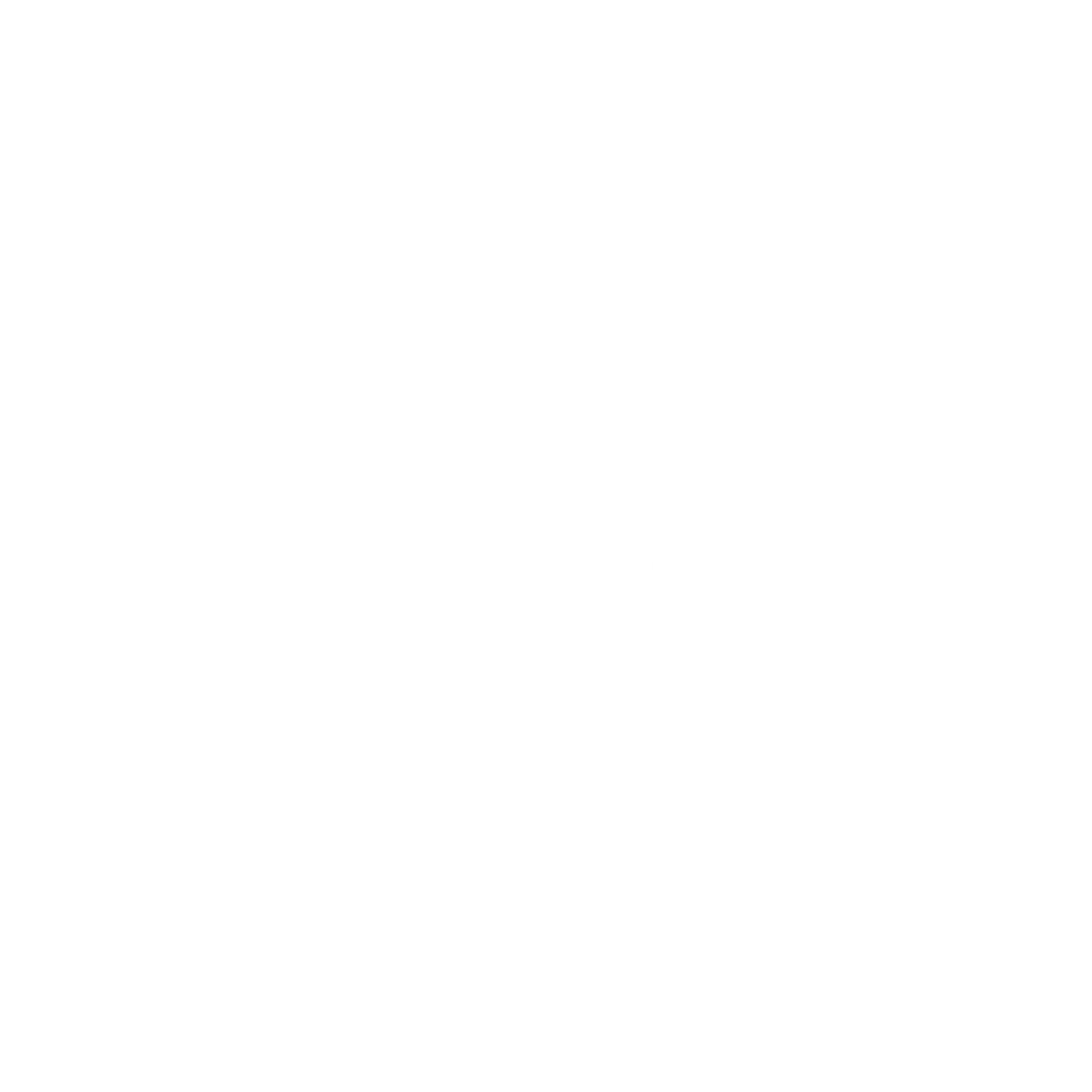
Arthrex
We have two P4K systems, which we use as our production machines. We are producing four parts at any time on those machines, so they run all day and all night, every day. We do 100 percent inspection, 100 percent of the time, and across the thousands of parts we’ve created we haven’t once had a deviation (from the model.)