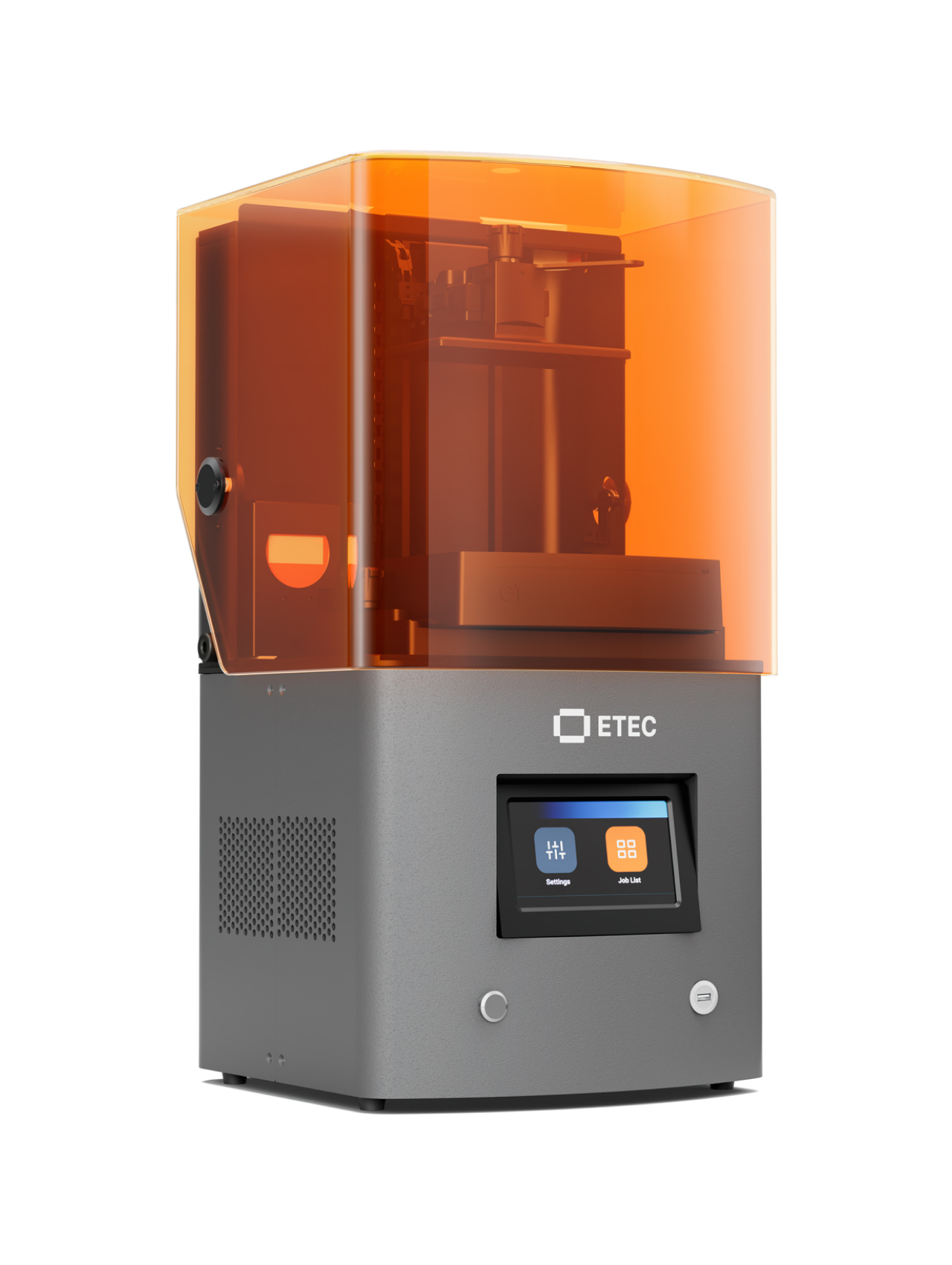
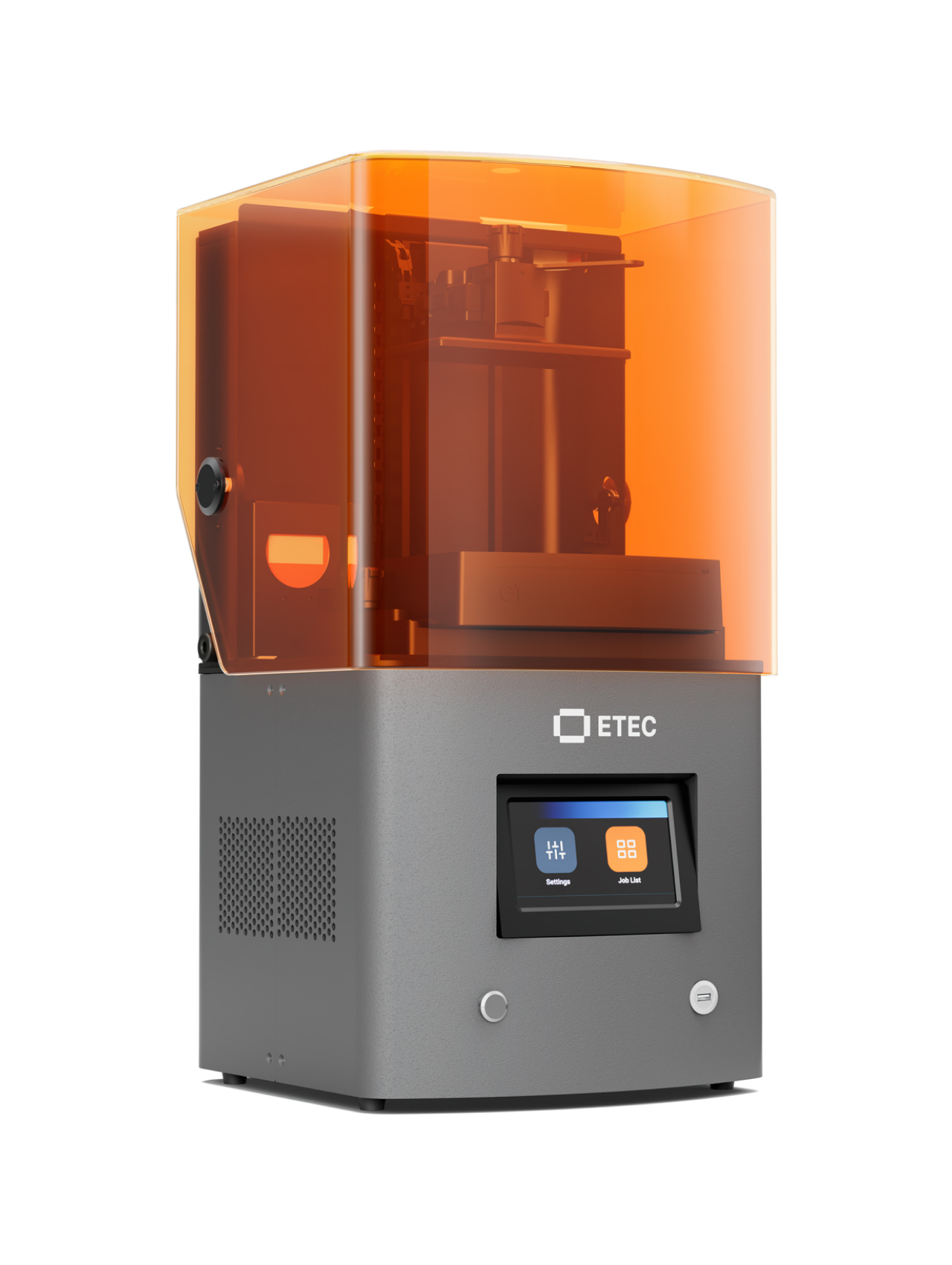
Envision One
• Overview
The Envision One features patented CDLM (continuous digital light manufacturing) technology, which enables the ability for continuous printing. With little to no delay between layers, the Envision One delivers exceptional speed, print resolution, surface finish, and part properties.
High-speed continuous printing
Finish an entire 3L build volume in just 4.5 hours – 30% faster than competing systems and 10x faster than desktop SLA.
Best-in-class part performance
The Envision One leverages long-chain polymer chemistry to produce strong, stable parts. The result is isotropic parts suitable for end-use applications and capable of standing up to the most demanding conditions.
High accuracy and resolution
Featuring patented “domeless” printing technology, the Envision One eliminates any concerns about how “doming” may impact accuracy on the Z axis. High-resolution (60 um XY) printing and patented pixel tuning technology make it easy to create fine features and smooth surface finishes suitable for end-use parts.
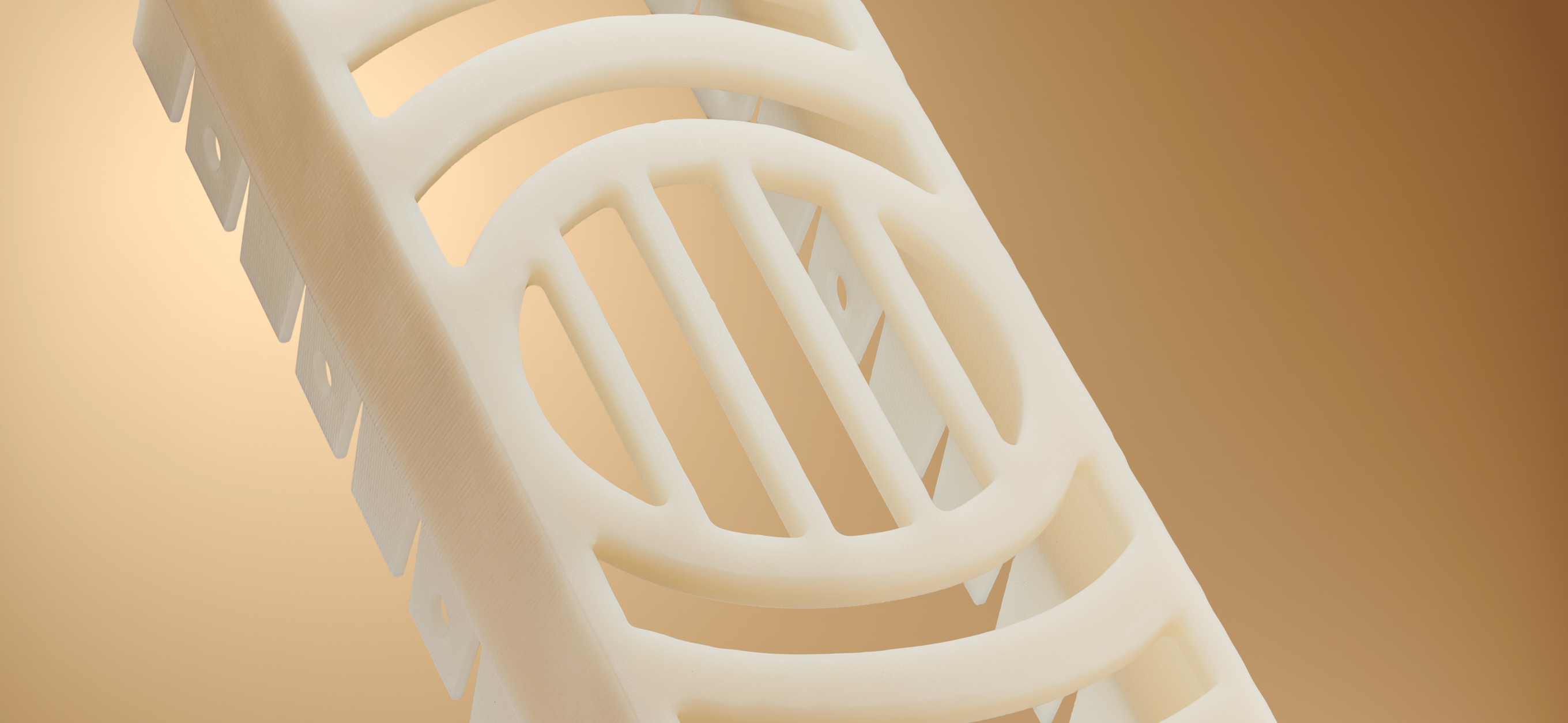
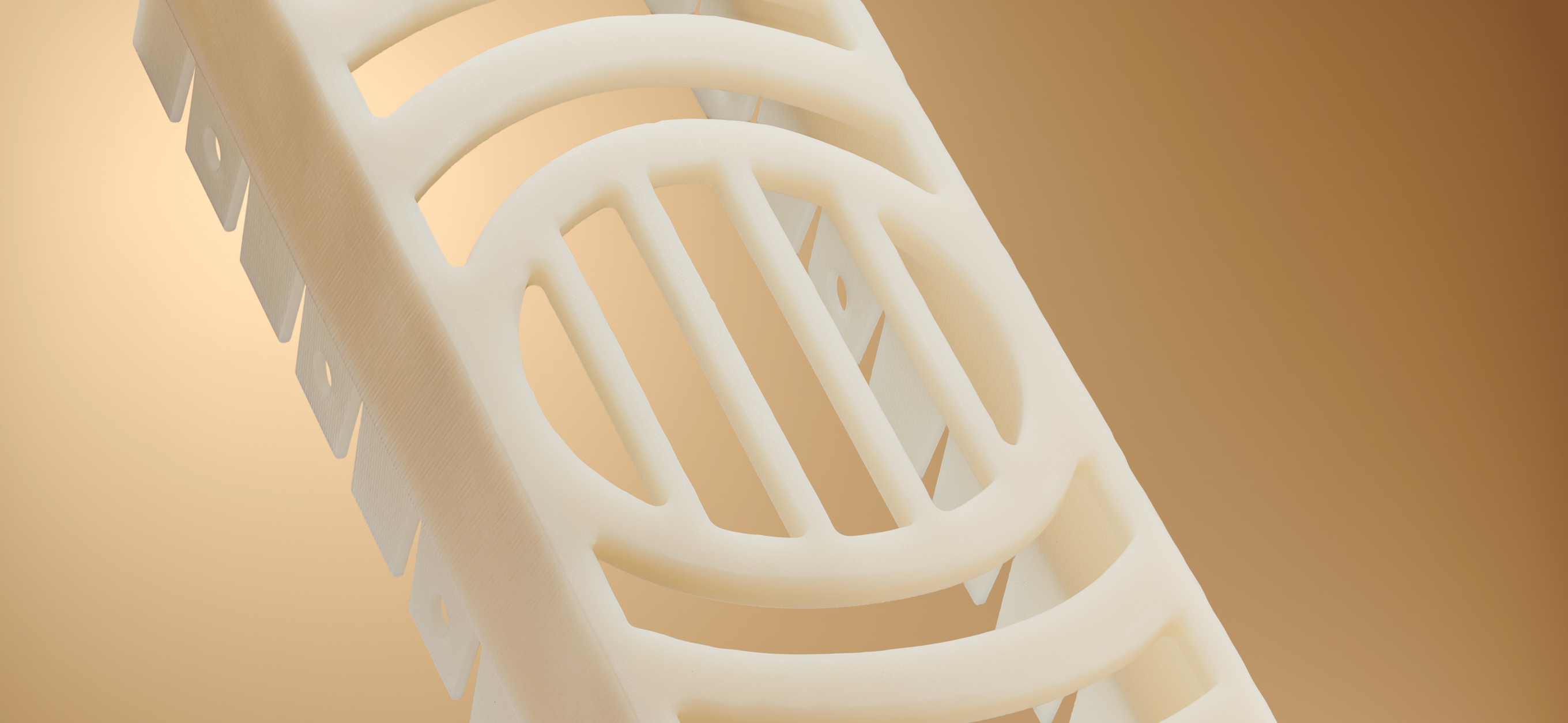
High-speed continuous printing
The cDLM process allows for continuous printing without the need to peel each layer off the film after it is polymerized.
A ‘dead zone’ is formed by flowing a thin layer of oxygen above the film of the printing bed. Within this ‘dead zone’ the polymerization process is inhibited ensuring the layer being printed adheres to the layer above and not the printing bed film. This ‘dead zone’ is what enables continuous printing, where the build plate can continually move in the Z axis, leading to faster, more reliable prints.
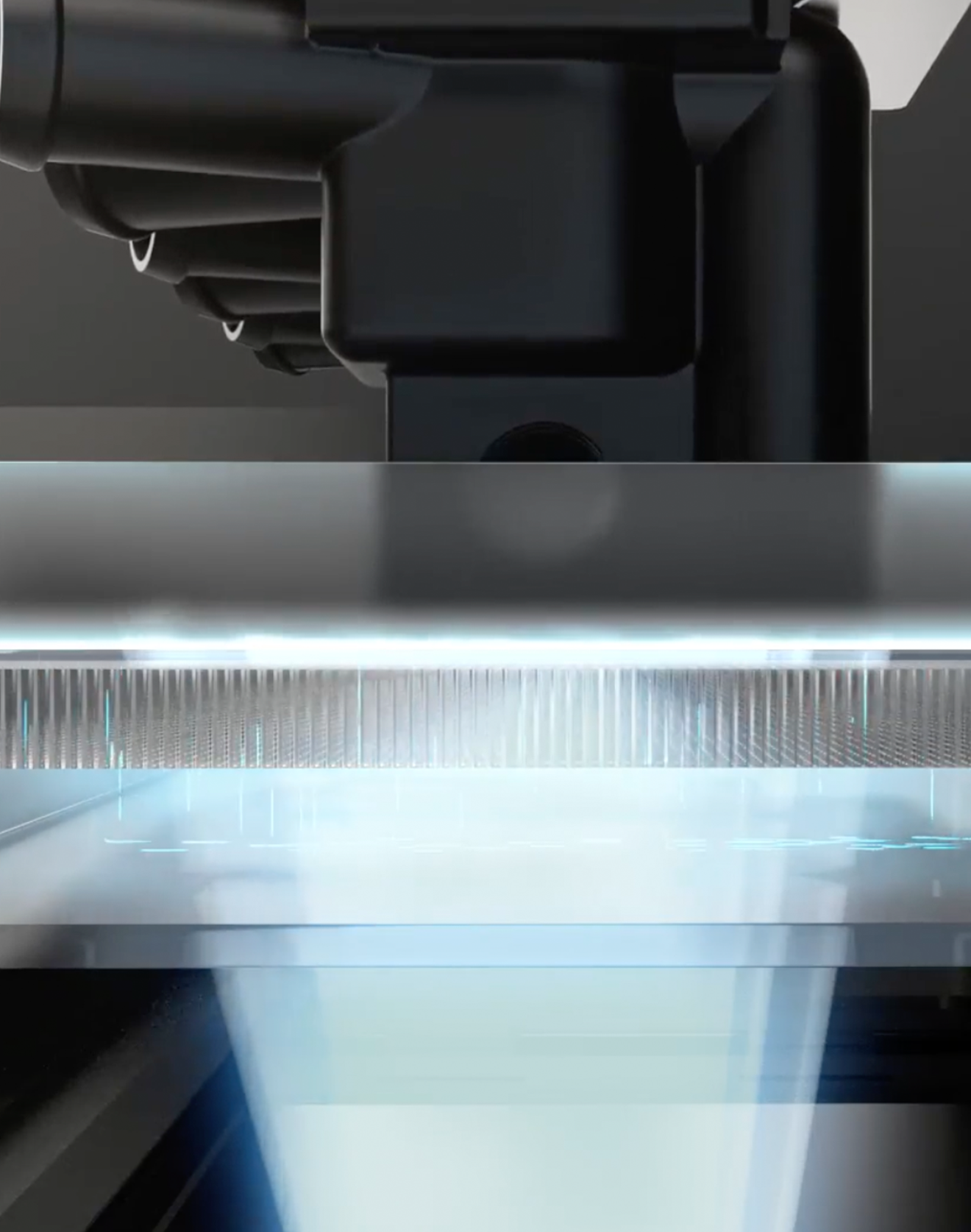
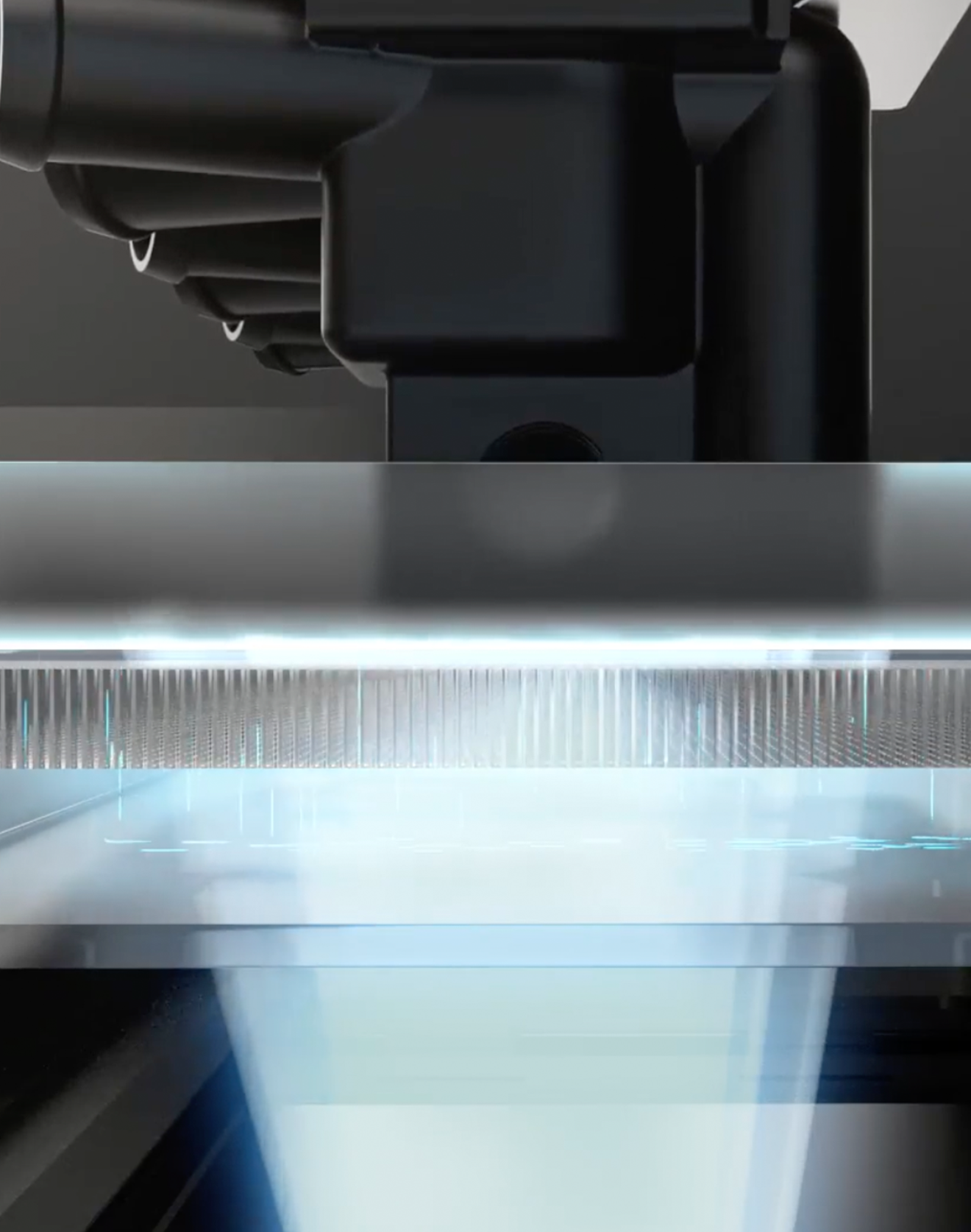
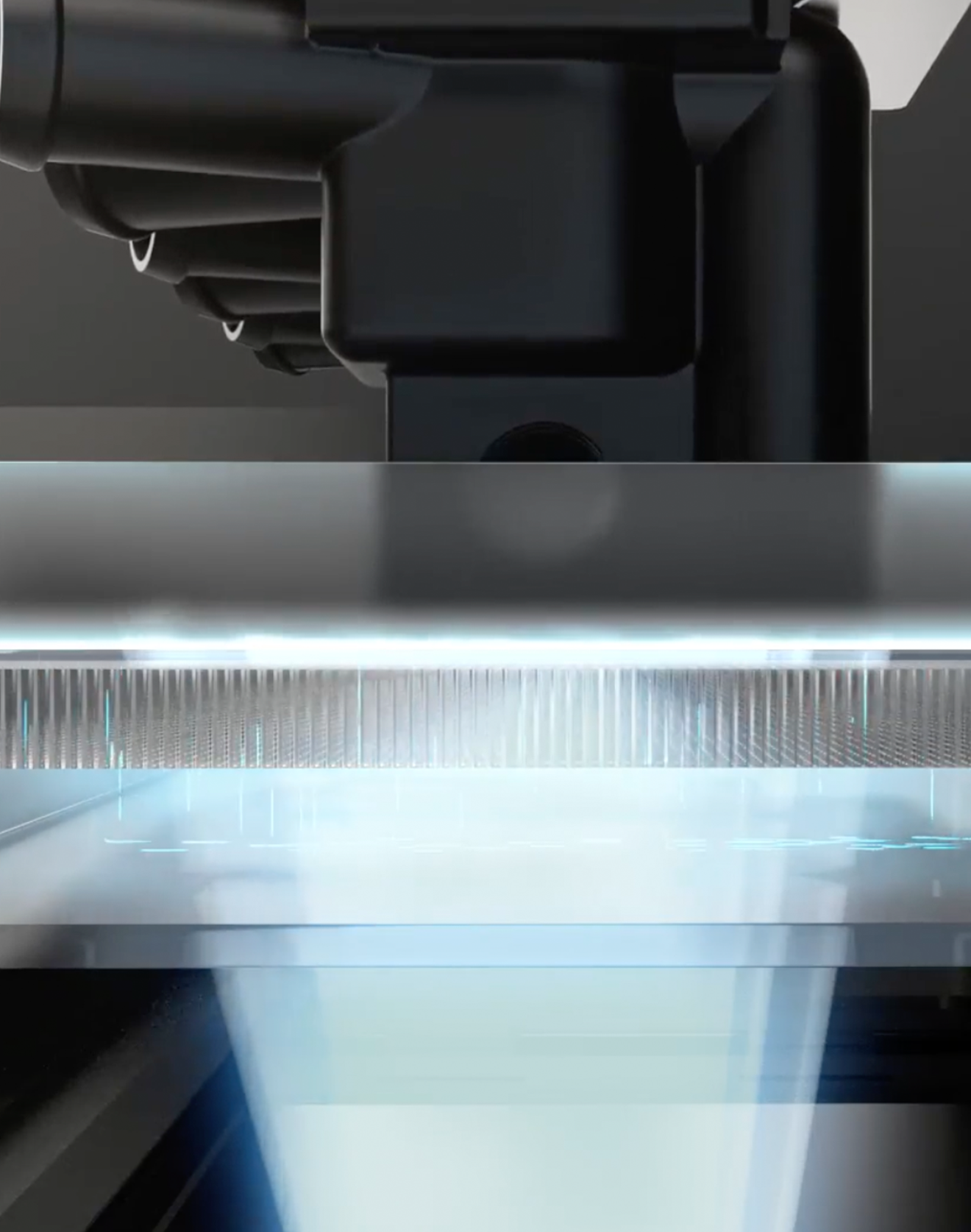
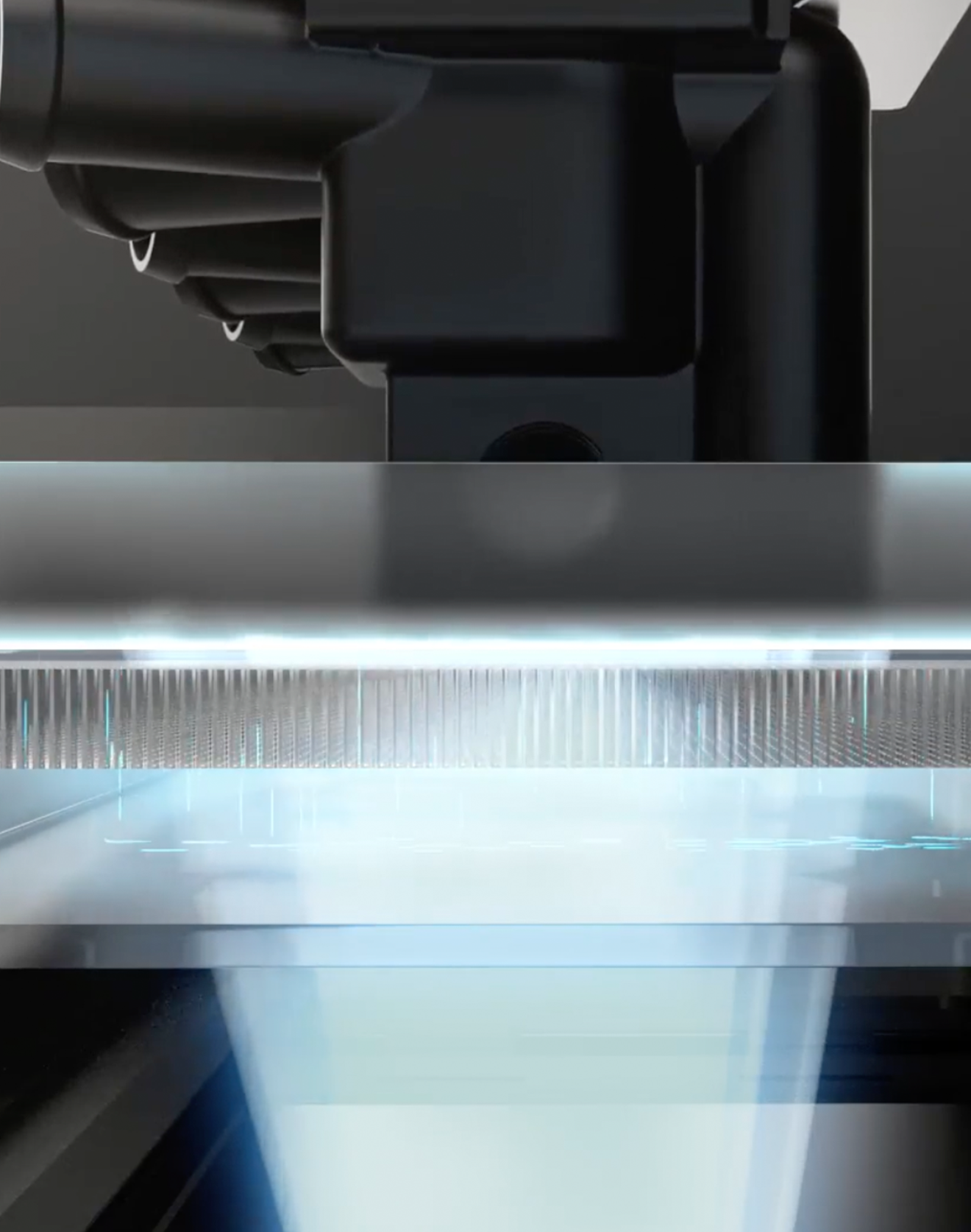
Best-in-class part performance
The Envision One cDLM produces end-use parts with properties that meet or exceed that of traditionally manufactured plastic components, such as injection molded plastics
Unlike most plastic additive manufacturing methods, parts created via CDLM are made up of entangled long-chain polymers, making them fully isotropic. This is vastly different from processes like FDM, which create anisotropic parts with few, if any, polymer chains between each layer. To create those long-chain polymers, printers must be able to process highly viscous resins which require large amounts of power to polymerize. Their high viscosity means these resins cannot be jetted (PolyJet), and would take too long to process with vector based polymerization methods (SLA).
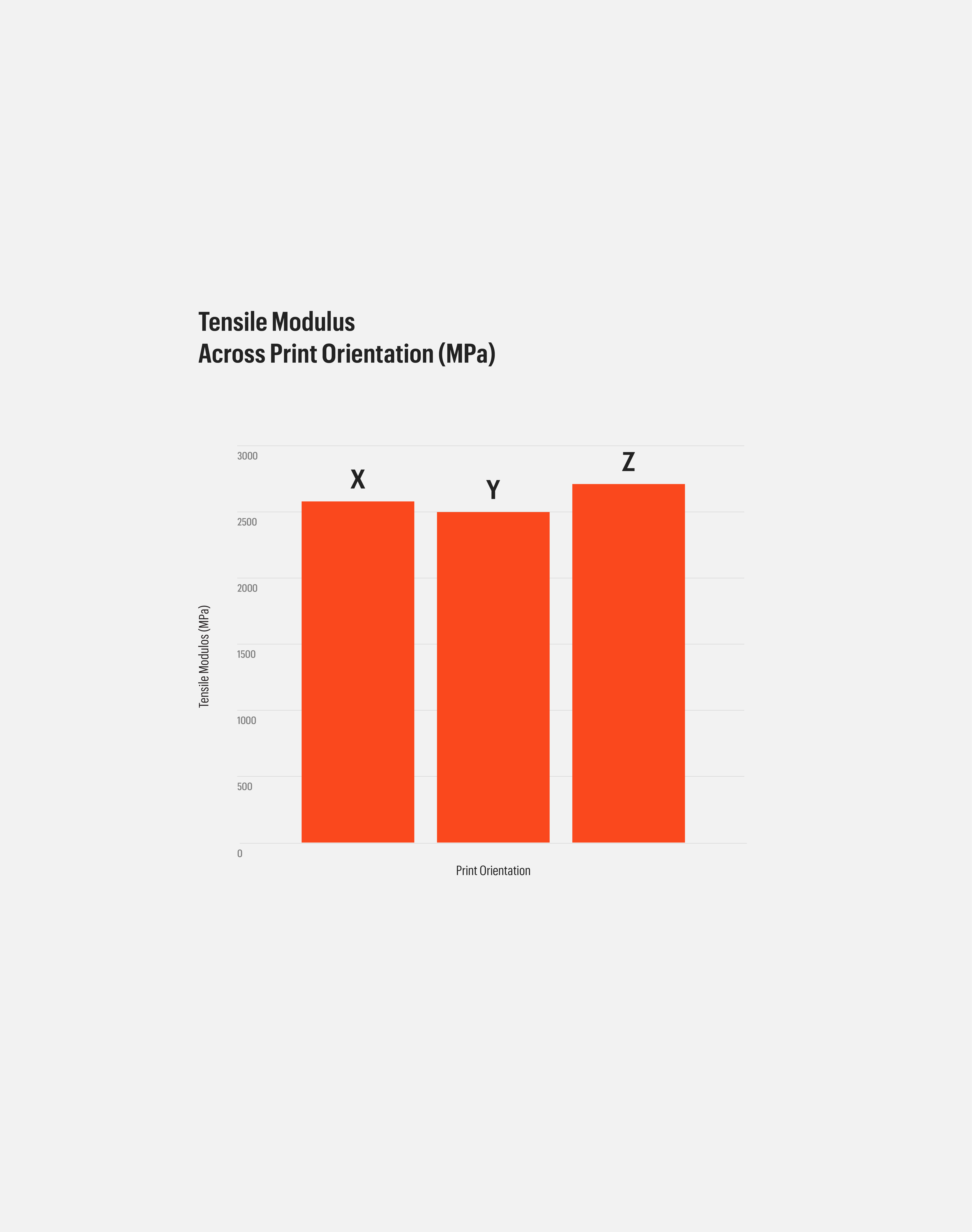
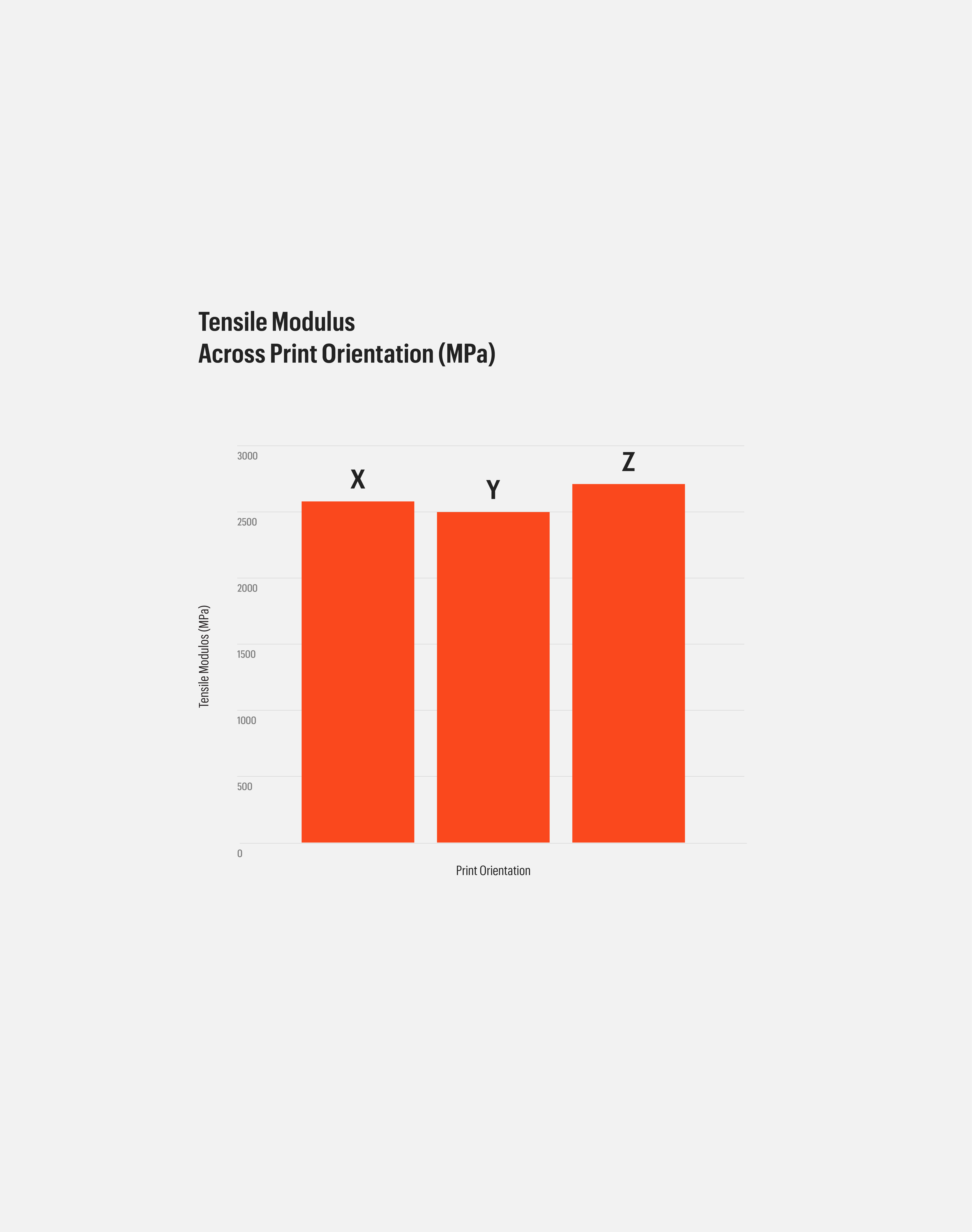
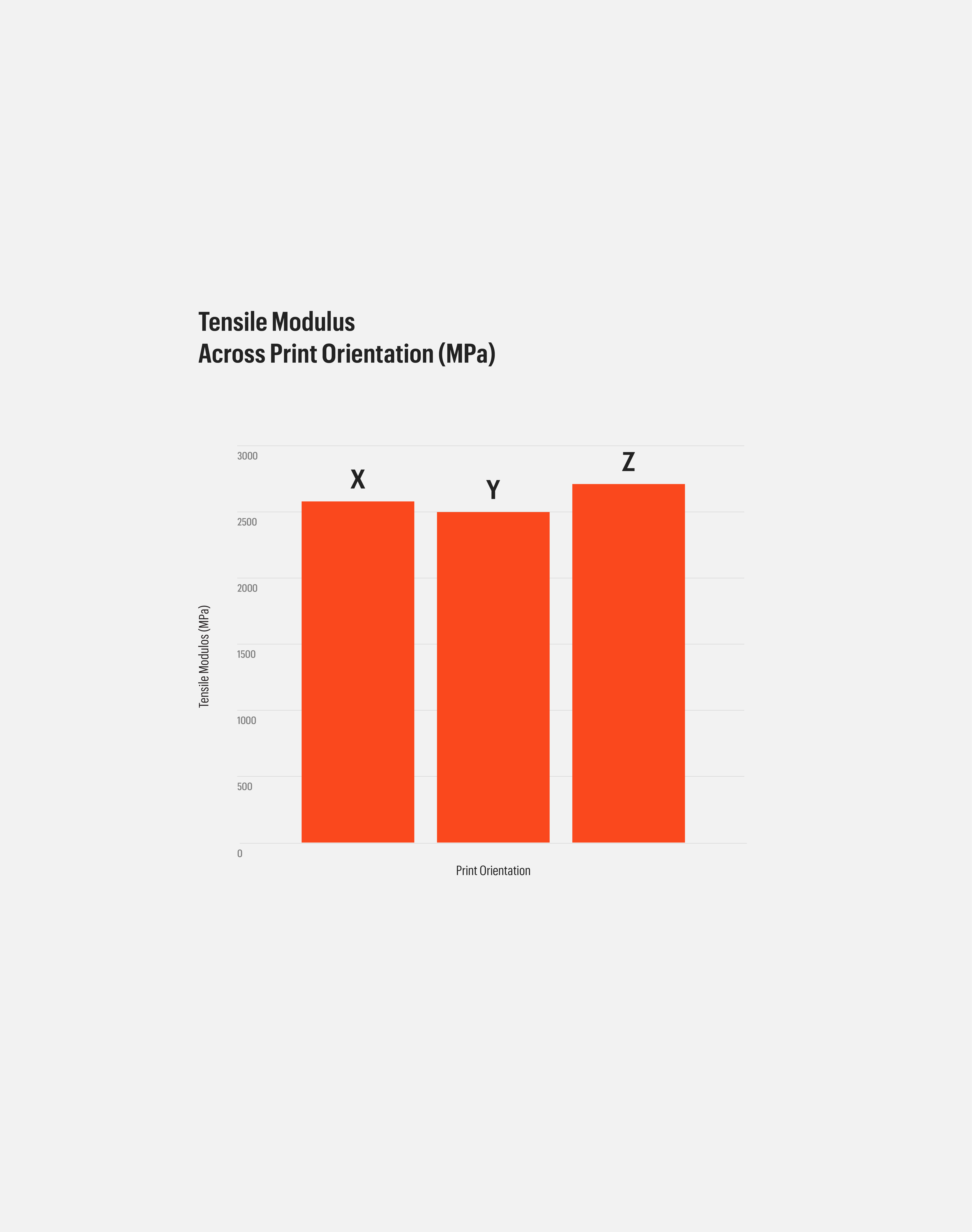
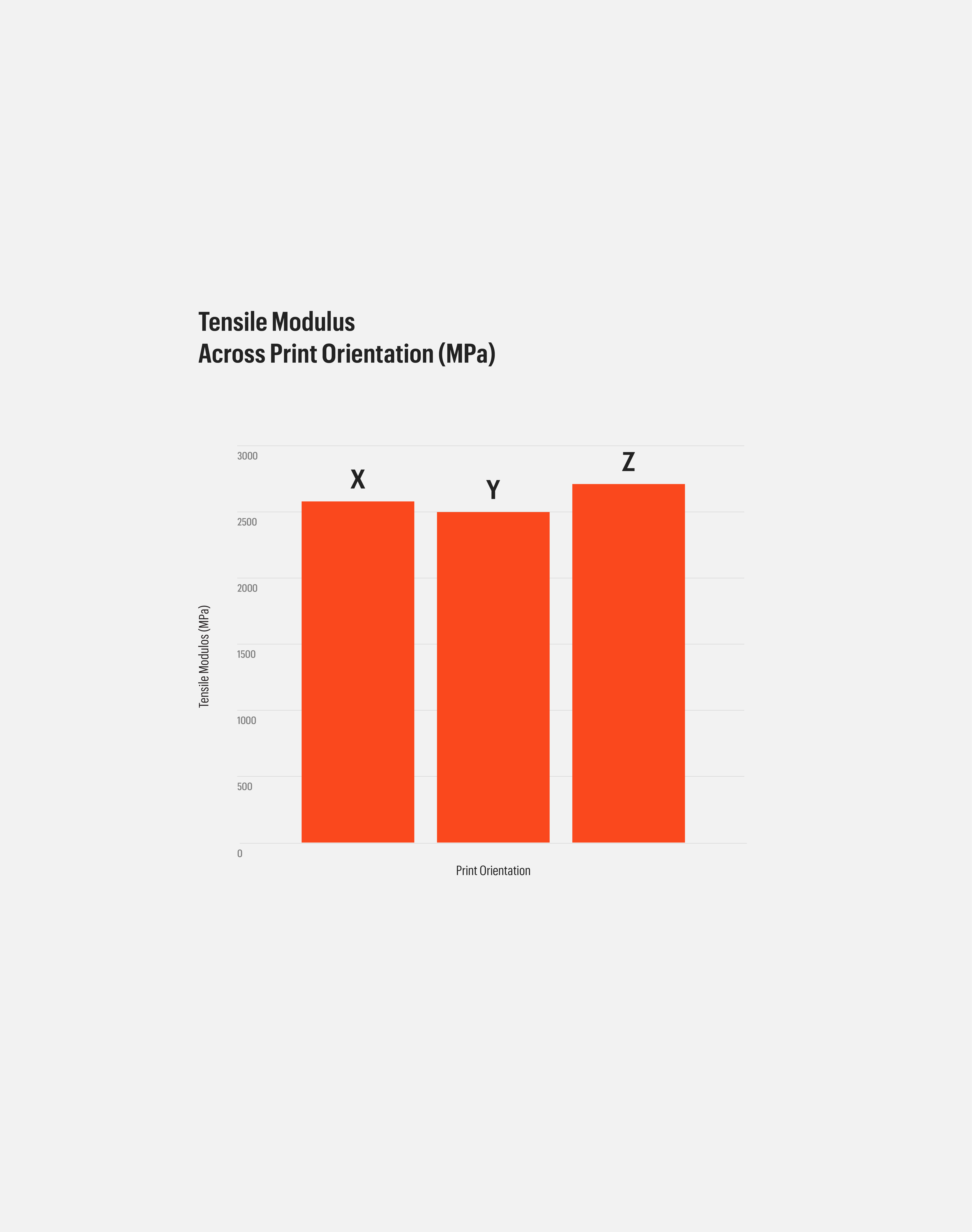
High-resolution printing
The Envision One cDLM delivers best in class part resolution and accuracy to print incredibly crisp features and hold tightest tolerances.
DLP is known for having incredibly high resolution parts and the EnvisionONE CDLM takes accuracy to new heights.
By using industrial DLP chips, verus cheaper consumer grade chips, and a custom designed optical train enable high contrast and minimal distortion for the projected picture resulting in accuracy down to the micron level.
The cDLM domeless printing process eliminates the “dome” effect to deliver incredible Z accuracy.
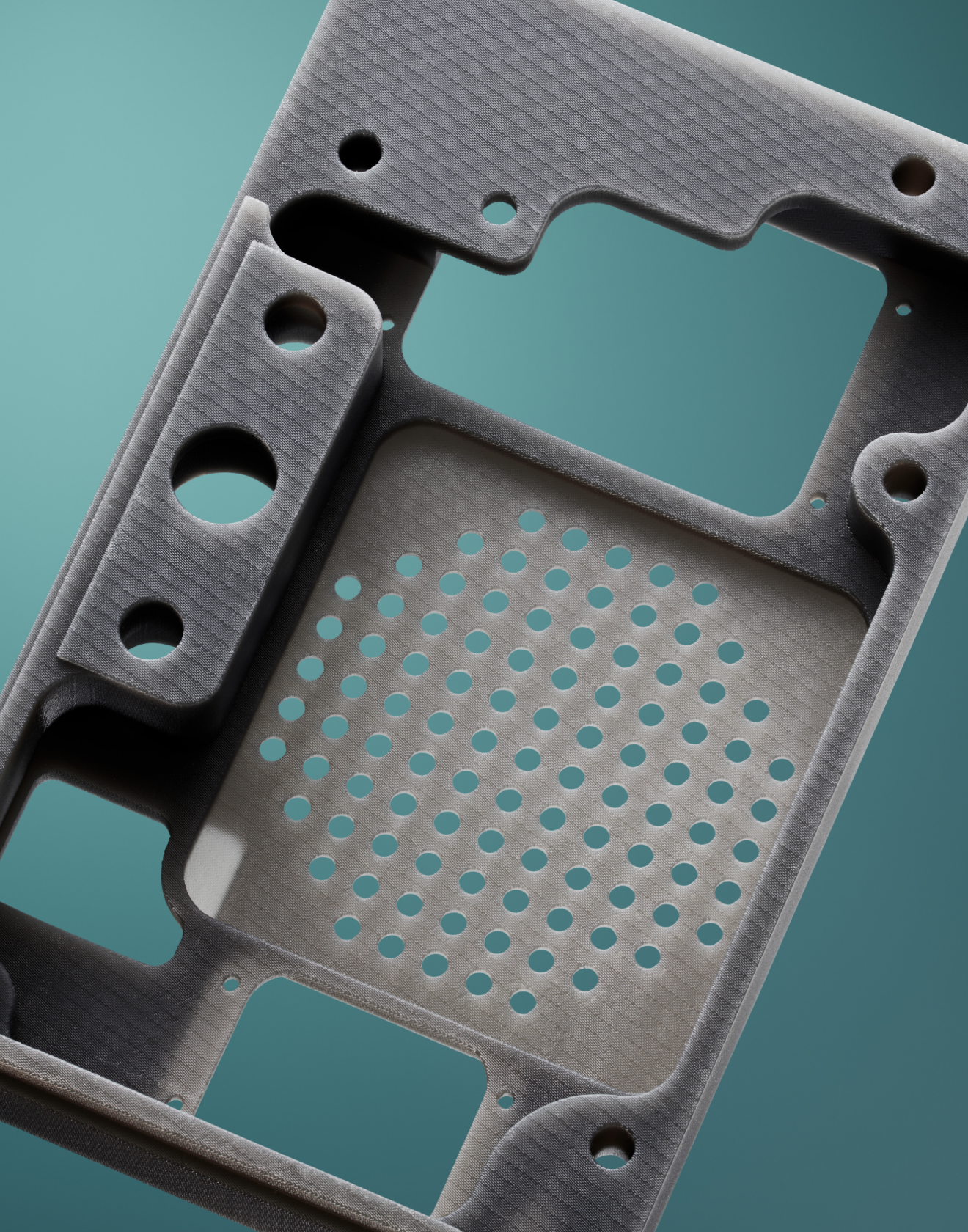
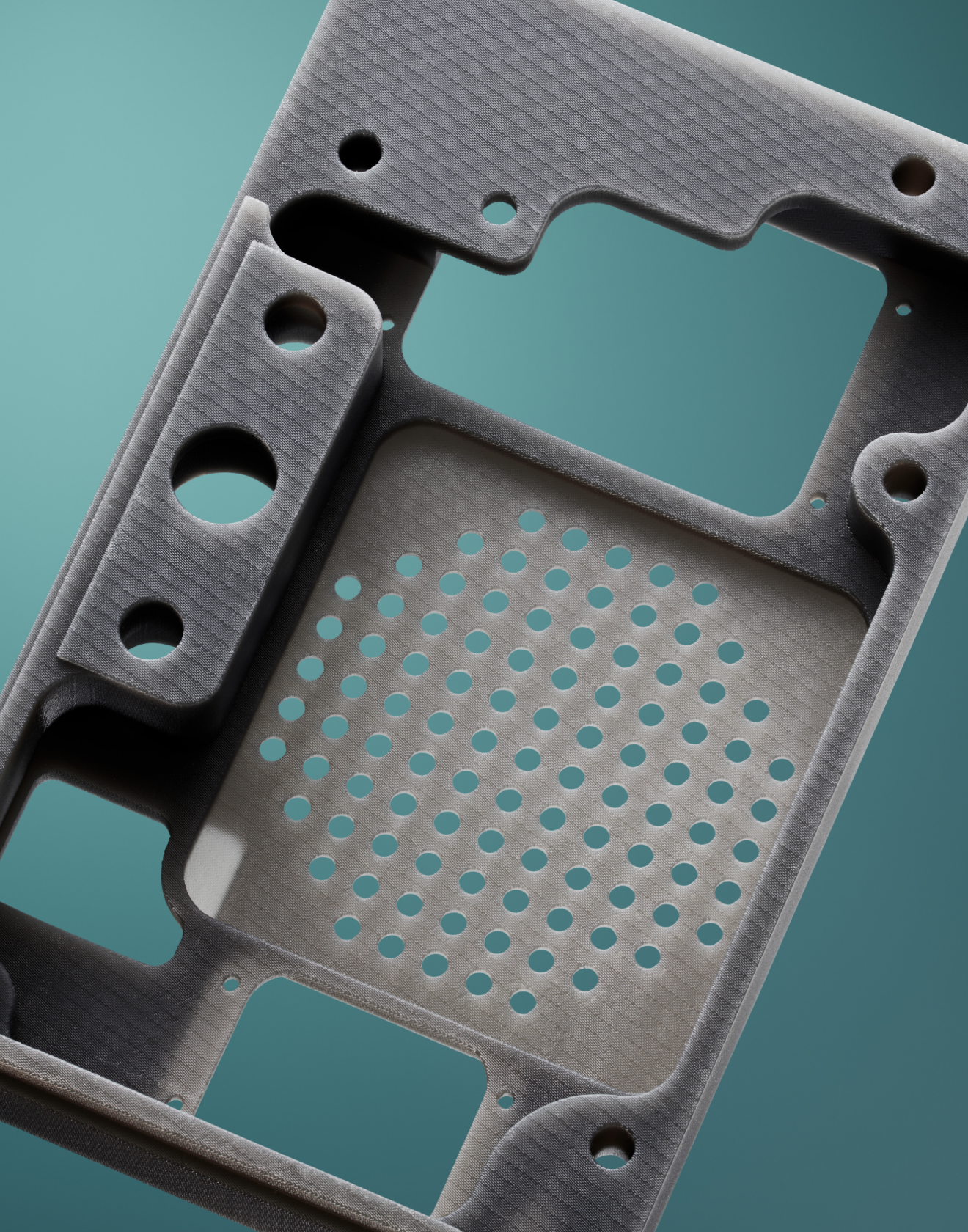
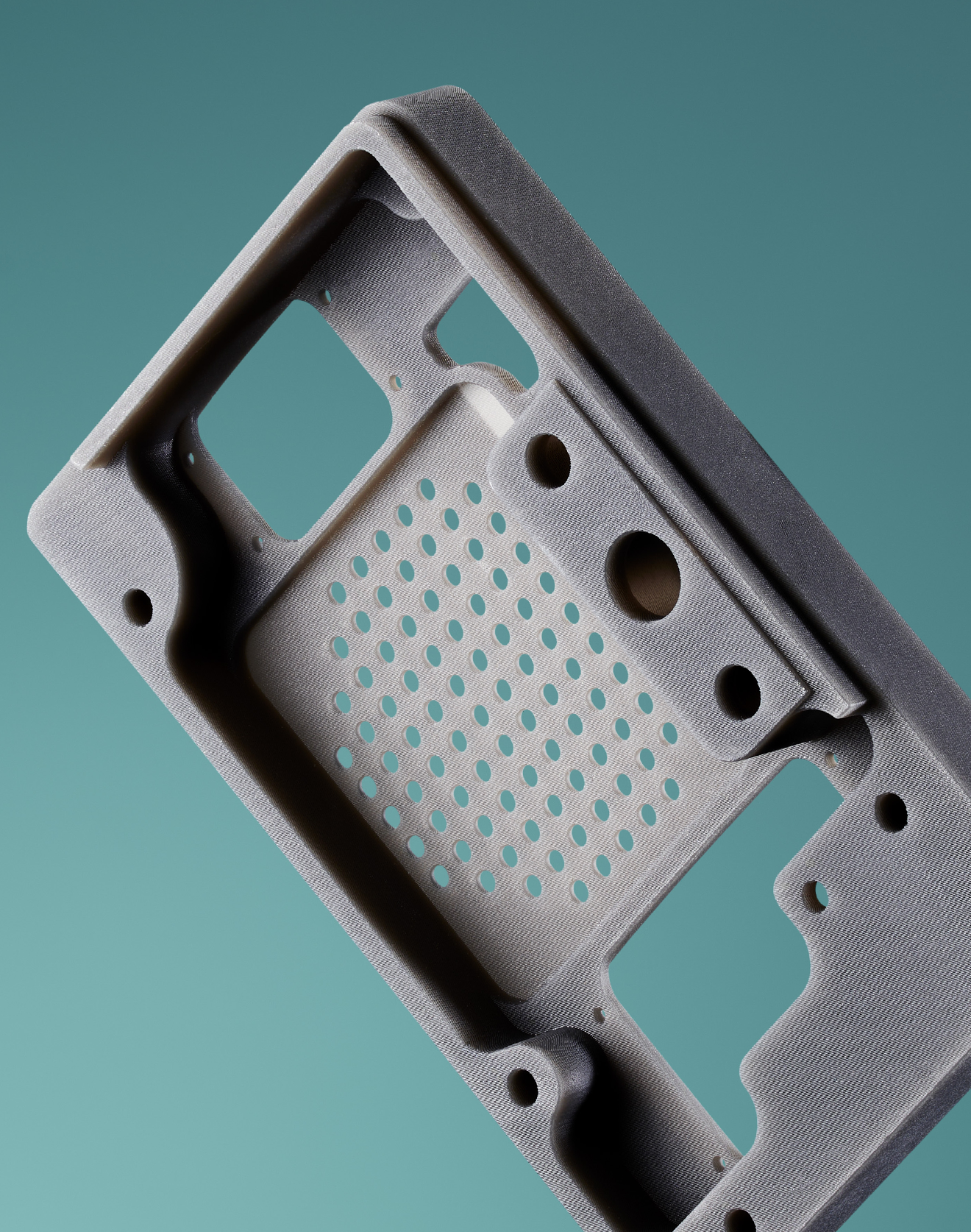
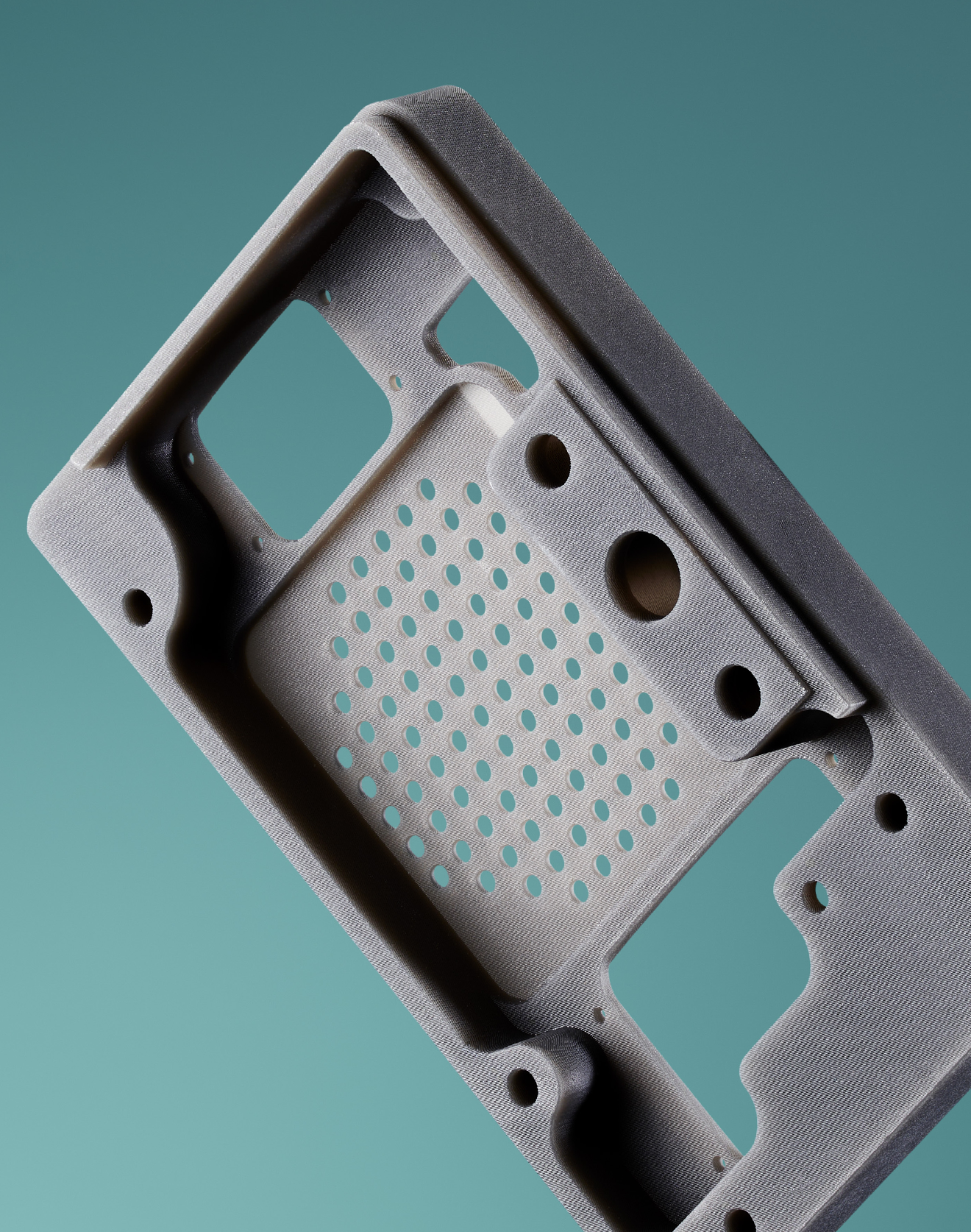
Easy to use software
The brains of the Envision One cDLM is EnvisionONE RP which streamlines the entire fabrication process, ensuring optimal part orientations, print settings, and printer productivity.
Intuitive, easy-to-use Envision One RP software automates support generation and part orientation, while an integrated file repair tool patches meshes and readies the parts for print. Cloud software allows users to remotely manage the system, send jobs to multiple printers and monitor job progress, while over-the-air software and firmware updates ensure users have access to the most up-to-date tools and processes.
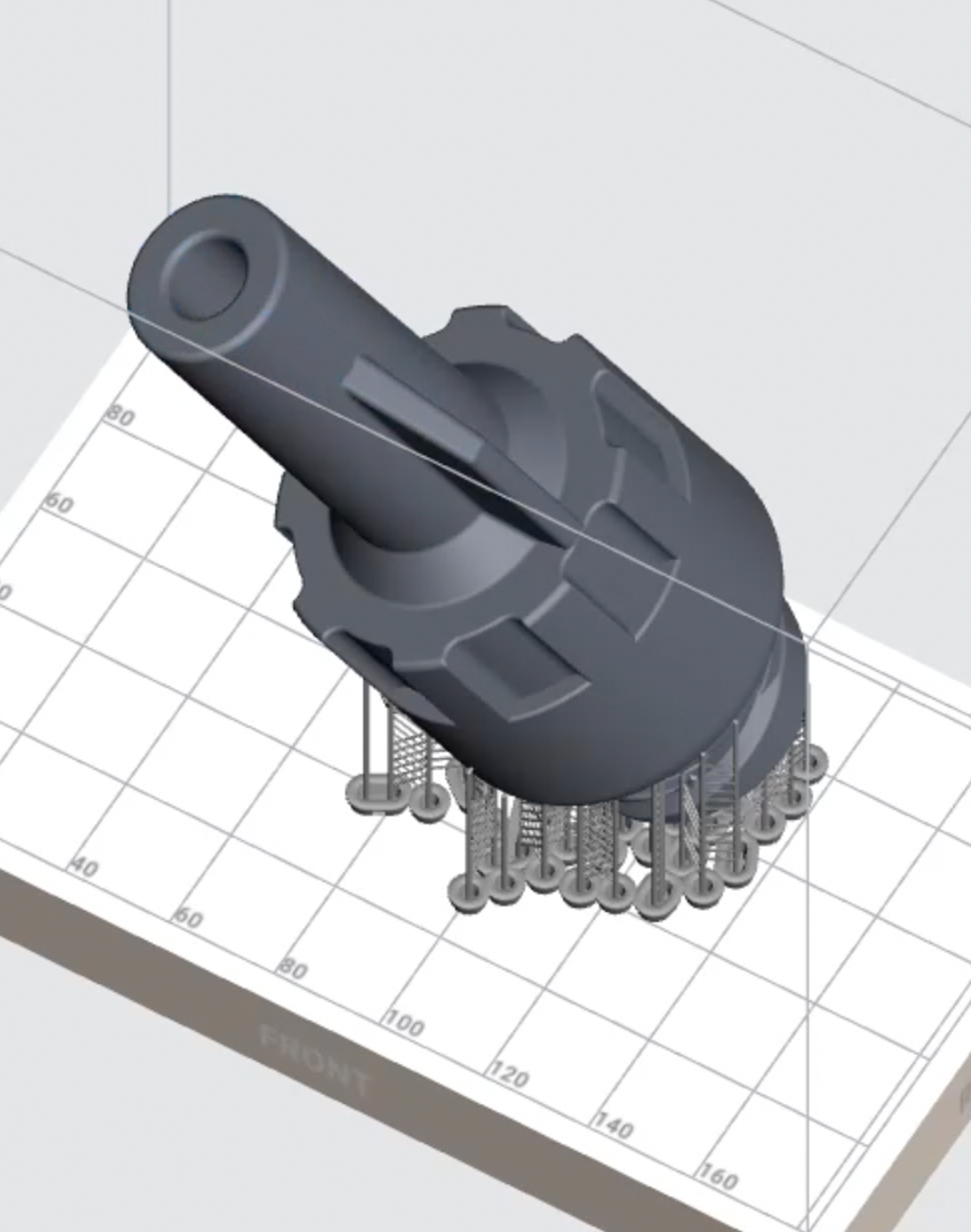
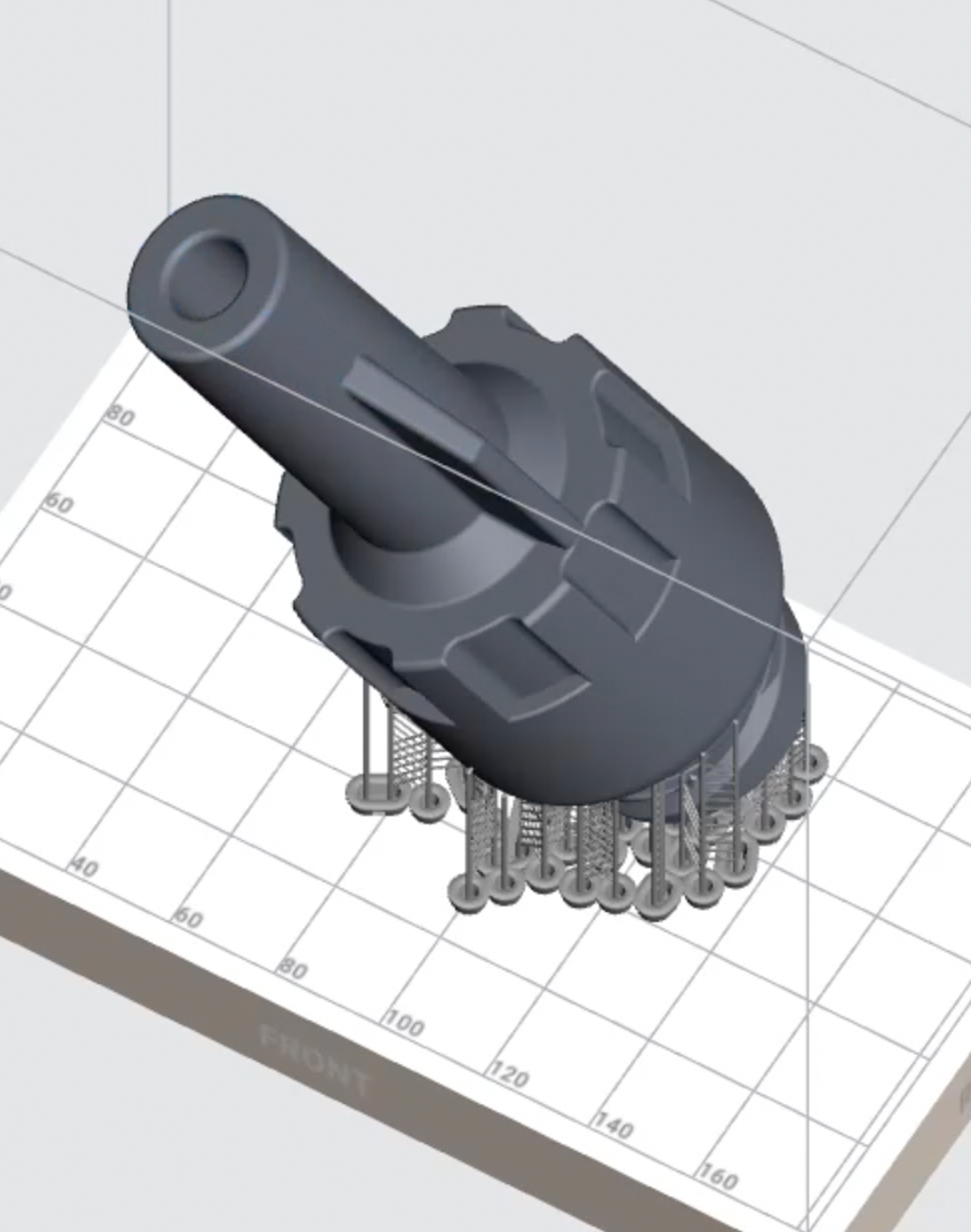
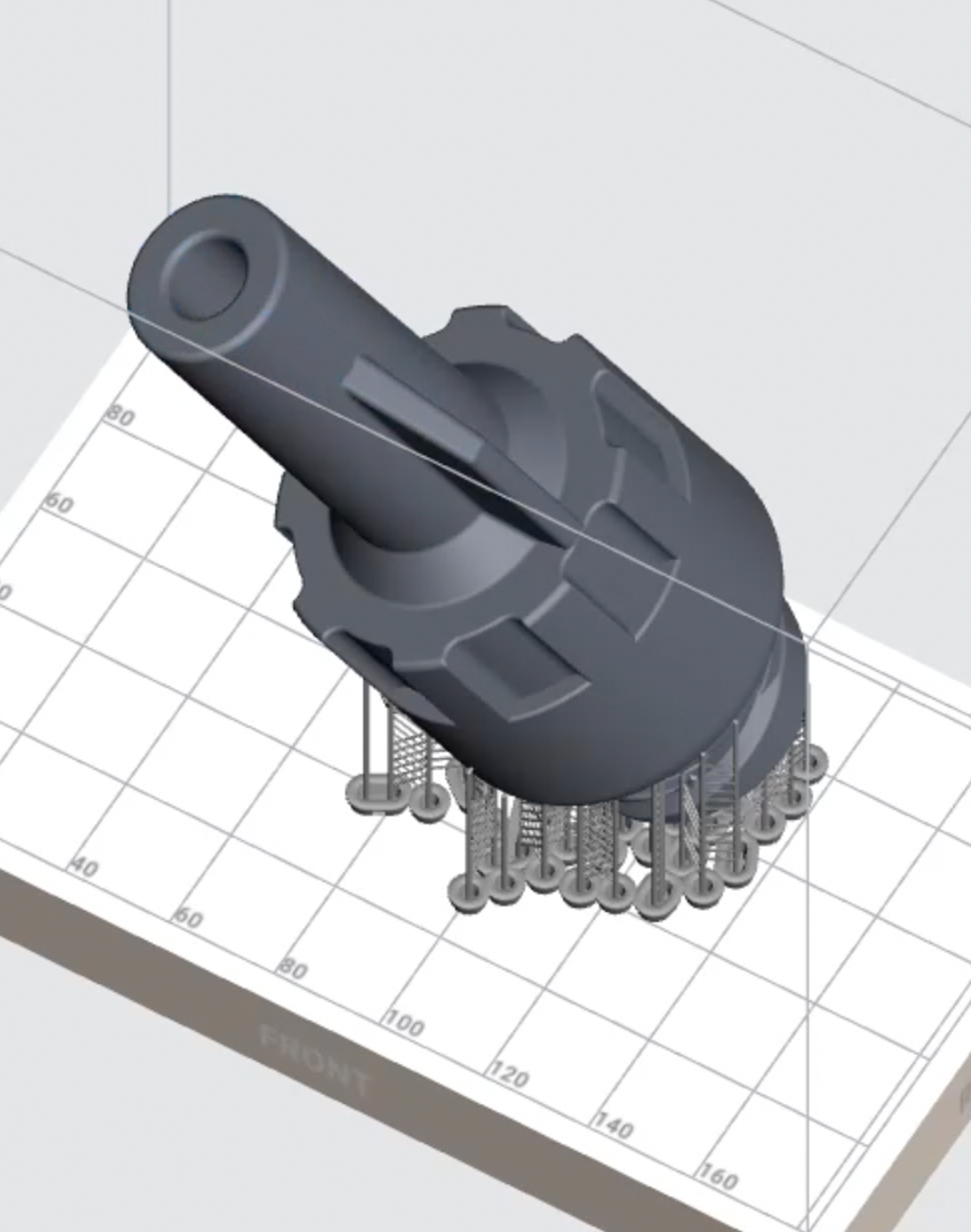
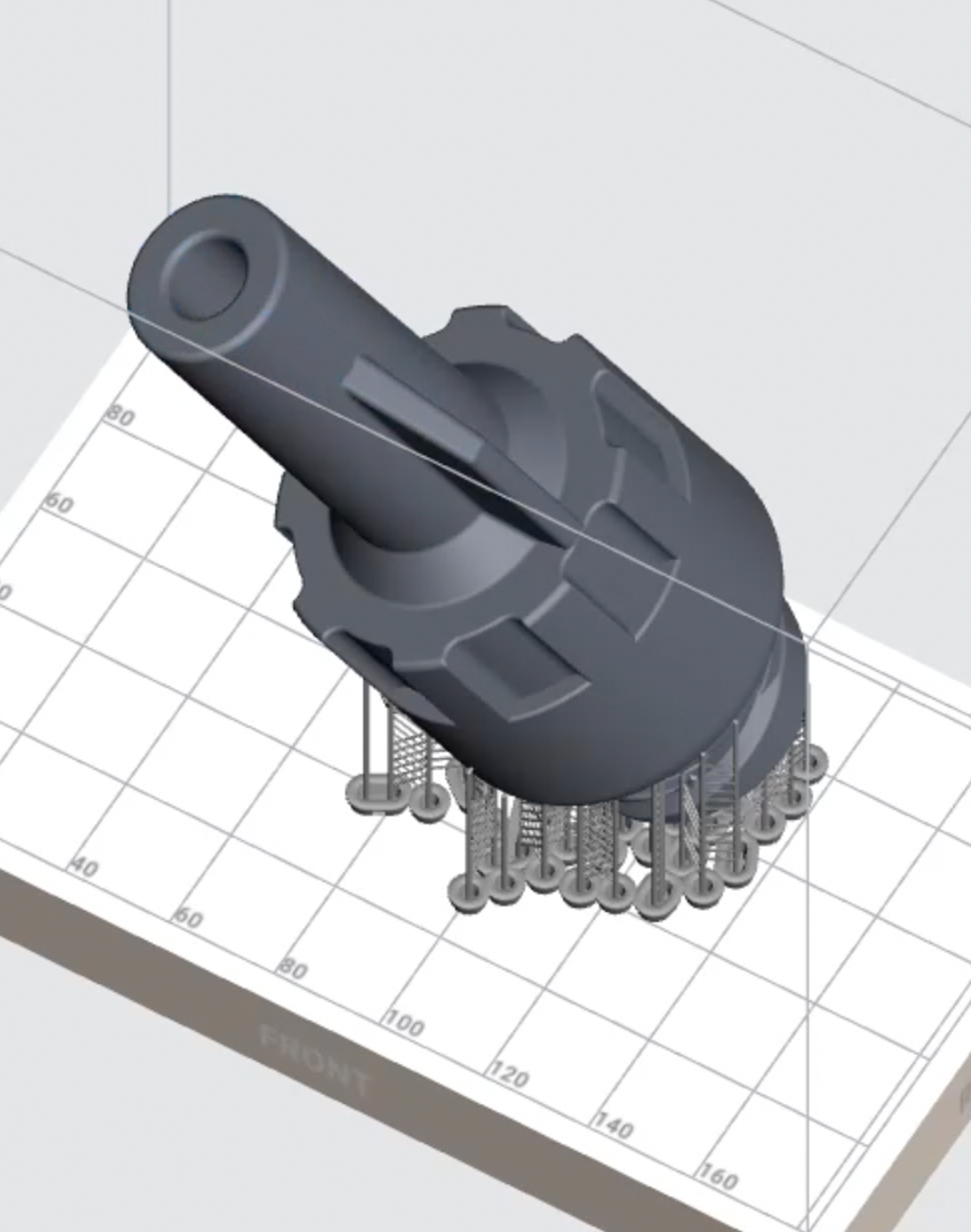
Customer Story
3D Composites
We make parts that go from outer space all the way to 10,000 feet below the ocean, and everywhere in between because of the versatility of the ETEC machines. In four months, we’ve probably done over 4,000 parts already. With the Envision One, we can hold tolerances down to two-tenths of a millimeter, and the build time is just phenomenal for 3D printing – there’s nothing anywhere close to it. We’re excited to grow with ETEC, the technology is amazingly repeatable.